Understanding Spray Drying: A Comprehensive Overview
What is Spray Drying?
Spray drying is a pivotal manufacturing technique that has been in use since the 1940s. It spans a multitude of industries, including industrial chemistry, pharmaceuticals, biotechnology, and food production. This method transforms liquid solutions, emulsions, or suspensions into dry powders through a streamlined process. By atomizing a liquid feed into fine droplets and subjecting them to a hot drying gas, the moisture is evaporated, resulting in a solid product.
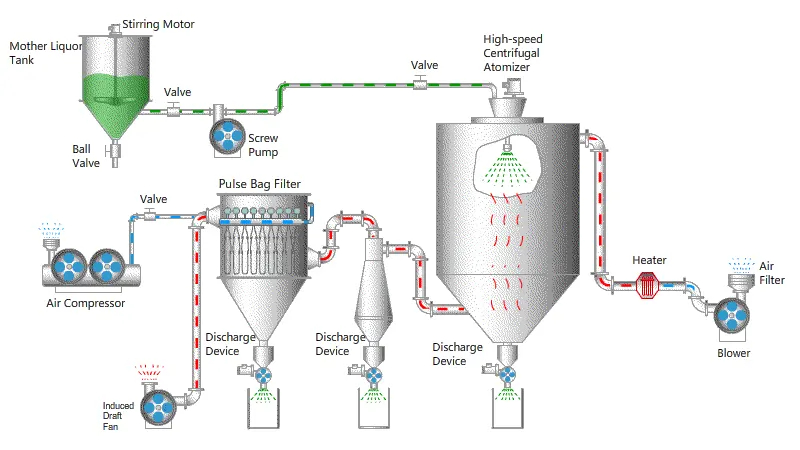
Advantages of Spray Drying
Spray drying is known for its high efficiency and rapid drying capabilities compared to other methods. This single-step process not only reduces weight and volume but also simplifies production, making it cost-effective and scalable. It is particularly adept at handling heat-sensitive materials, preserving the integrity of biologics, pharmaceuticals, and food nutrients. The resulting powder is often uniform and spherical, allowing for easy formulation into tablets or capsules without the need for additional milling. Furthermore, many temperature-sensitive compounds, including enzymes and proteins, can be spray dried while maintaining their activity. This technique can also be performed in inert atmospheres, ensuring product stability.
In contrast to freeze-drying, spray drying is quicker and more economical, as it eliminates the need for deep freezing and consumes less energy. Researchers have even explored using spray drying as an alternative to freeze-drying.
Laboratory Scale vs. Industrial Scale: Challenges and Benefits
While spray drying offers numerous advantages, it also presents challenges, particularly at the laboratory scale. Yield losses can occur due to product adhesion to the drying chamber walls and in exhaust air, with reported yields ranging from 20% to 70%. However, industrial applications typically see improved yields due to larger production volumes.
Laboratory-scale spray drying is limited in producing particles larger than 50 μm, which may impact subsequent scale-up processes, especially when dissolution rates are critical. On the upside, laboratory systems allow for quick handling of small sample sizes and shorter cleaning times, enabling more experiments in less time. The glass construction of these systems also permits real-time observation of the drying process, facilitating immediate adjustments.

Applications Across Industries
Spray drying has established itself as a preferred method for creating dry powders across various sectors due to its continuous, gentle, and scalable nature.
Food Industry
In food technology, spray drying is employed to produce items like coffee, powdered milk, and nutritional supplements. This method ensures good solubility, minimizes flavor loss, and retains the nutritional content of heat-sensitive foods.
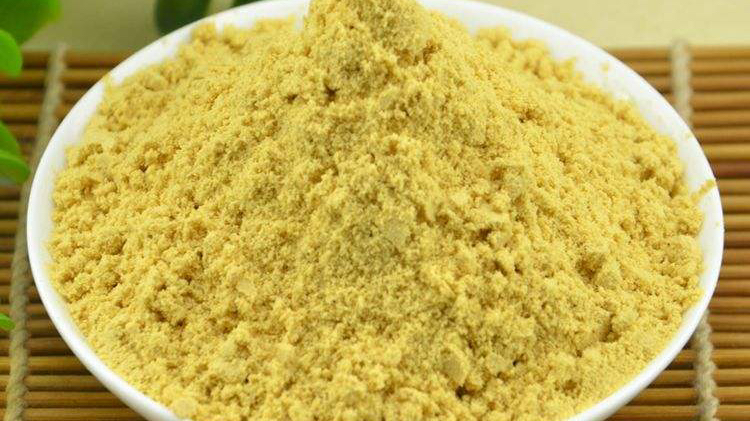
Chemical Industry
In the chemical sector, spray drying is utilized for cosmetics, detergents, and pigments. It enhances particle size reduction for dyes, improving their dispersion in paints, and is instrumental in creating free-flowing powders for advanced materials.
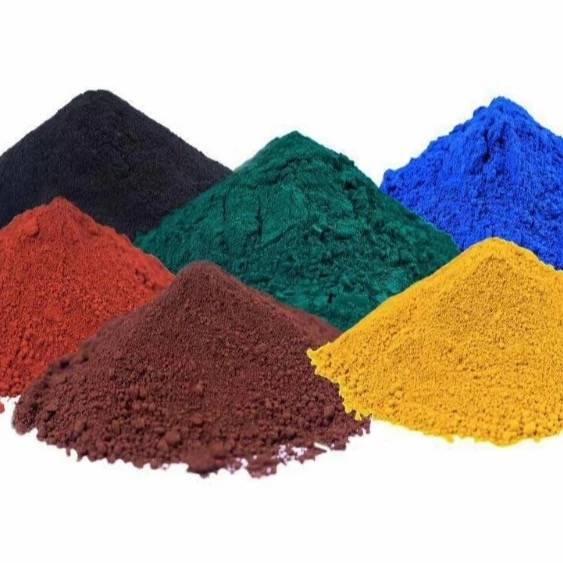
Pharmaceutical Industry
Spray drying is a common technique for obtaining granulated substances in pharmaceuticals, enabling efficient encapsulation and controlled release of active ingredients. It is particularly effective for producing solid formulations from liquid solutions.
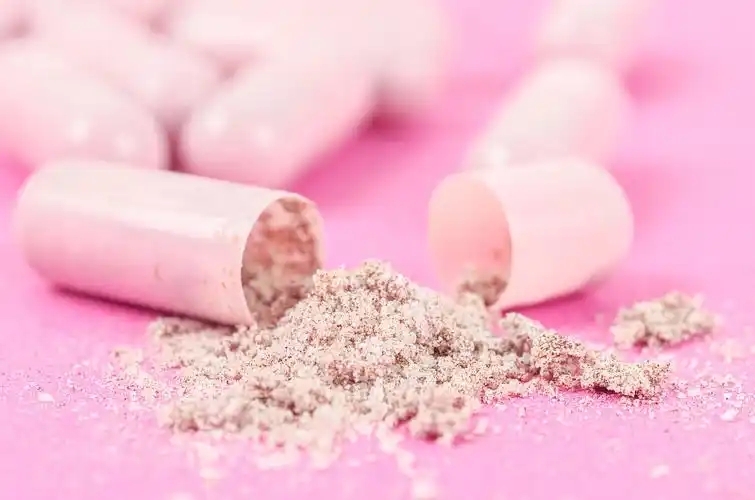
The Spray Drying Process
The spray drying process involves dissolving or emulsifying the core substance in a solvent. The mixture is then atomized and introduced into a drying chamber, where hot air facilitates solvent evaporation, resulting in solid particles that are collected using centrifugal forces.
Particle Morphology
The spray drying process can yield various particle shapes, including dense, hollow, and porous structures. Generally, slower drying leads to more compact particles, while faster drying results in hollow formations.
Optimizing the Spray Drying Process
Successful spray drying relies on understanding the interplay of material properties, equipment design, and process parameters. Key factors affecting product quality include:
- Feed Rate: Higher gas flow rates produce smaller droplets and particles.
- Solid Concentration: Increased solid concentration results in larger, more porous particles.
- Inlet Temperature: Higher temperatures can boost throughput but may risk degrading sensitive compounds.
- Outlet Temperature: Determined by the heat and mass balance, it is influenced by various parameters and cannot be directly controlled.
- Residence Time: Essential for complete drying, typically ranging from 0.2 to 0.35 seconds in lab-scale dryers.
- Glass Transition Temperature (Tg): Understanding Tg is crucial to prevent stickiness and ensure product quality during processing.
By adhering to these guidelines and continuously refining the process, manufacturers can achieve optimal results in spray drying.
This comprehensive overview of spray drying highlights its significance, advantages, and applications across various industries. By understanding the intricacies of the process, businesses can leverage this technology to enhance product quality and efficiency.
Contact us for customized solutions from our expert team