Spray Drying: Types, Benefits, and Applications
Spray drying is an industrial process used to convert liquid materials into powders or granules in a single step. This involves atomizing the liquid into fine droplets and rapidly drying them in a hot air stream, resulting in a powder that is easy to transport and package. Due to its efficiency, versatility, and ability to maintain consistent product quality, spray drying is widely utilized in industries such as food, pharmaceuticals, and chemicals.
Let’s begin with a brief history of spray drying!
History of Spray Drying
Spray drying was first applied in the 19th century by a French engineer who developed a method for drying wine yeast. The process gained widespread use in the mid-20th century when the first industrial spray dryers were introduced. Initially, nozzle atomizers were used, but rotary atomizers were later developed to improve efficiency. Since then, the technology has evolved to accommodate a wide range of industrial applications.
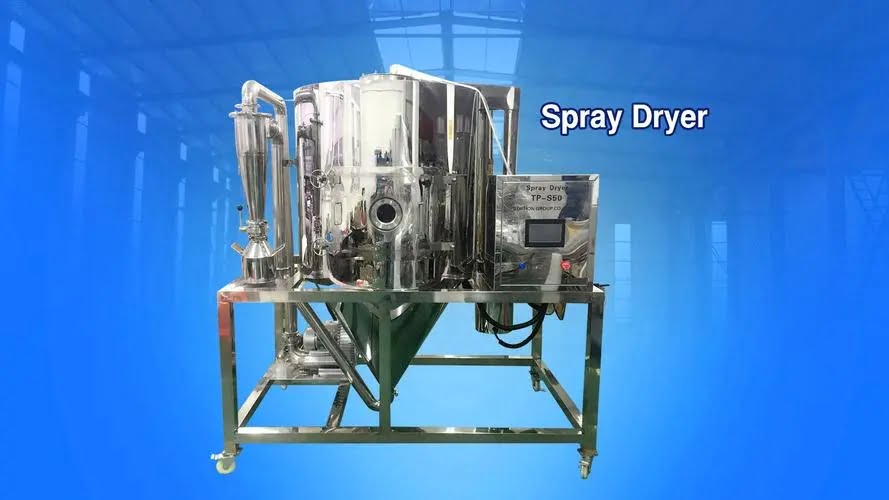
How Spray Dryers Work
The typical spray drying system includes:
- Feed Preparation: Ingredients are mixed, viscosity is adjusted, and the mixture is homogenized to create a liquid feed.
- Atomization: The liquid is pumped into a nozzle or spinning disk, breaking it into fine droplets.
- Drying: The droplets are dried in a chamber by a hot air stream, with parameters like temperature and airflow carefully controlled to achieve desired particle size and moisture content.
- Collection: The dried powder is collected using systems like cyclones or bag filters for packaging or further processing.
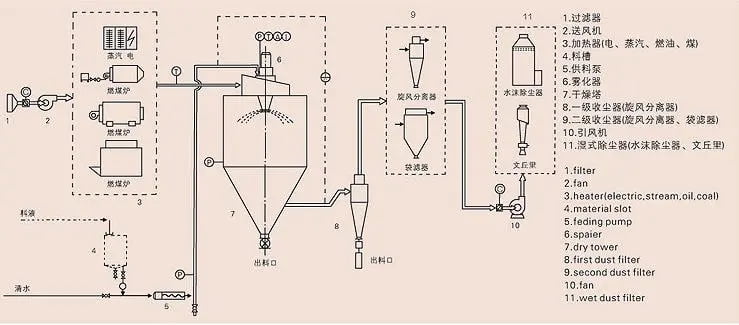
The rapid evaporation of liquid droplets in hot air is the key to the spray drying process. The drying rate is influenced by droplet size, temperature, air velocity, and the moisture content of the product.
Types of Spray Dryers
Several types of spray dryers exist, each designed for specific applications:
- Rotary or Centrifugal Atomizers: Use a spinning wheel to atomize liquids into droplets, suitable for high-viscosity feeds and a wide range of materials.
- Pressure Nozzle Atomizers: Use high-pressure pumps to create consistent, homogenous powders with narrow particle size distribution, commonly used in food and dairy industries.
- Two-Fluid Nozzle Atomizers: Utilize a pressurized gas (such as air or steam) to atomize the liquid, often employed in pilot-scale applications.
- Combination Systems: Combine spray drying with fluidized beds to improve efficiency and product characteristics, particularly for producing agglomerated materials.
- Closed-Cycle Systems: Designed for sensitive products or organic solvents, using nitrogen instead of air to prevent oxidation and enhance safety.
Advantages of Spray Drying
- Single-Step Processing: Converts liquids directly into powders in a single step, making it a cost-effective option for small-scale or pilot production.
- Flexibility: Suitable for a wide range of materials, from food and pharmaceuticals to chemicals and cosmetics.
- Consistent Product Quality: Produces uniform particles that are stable and easy to handle, with good flow properties.
- Preservation of Active Ingredients: Maintains the potency and efficacy of active compounds, ideal for pharmaceuticals and biopharmaceuticals.
- Contaminant Reduction: Reduces microbial contaminants, especially critical in food and pharmaceutical applications.
Industrial Applications of Spray Drying
Spray drying is used in diverse industries, such as:
- Food: For creating instant products like coffee, milk powder, and flavorings, while preserving flavor, aroma, and color.
- Pharmaceutical: For producing powders, granules, and tablets, as well as encapsulating active ingredients.
- Chemical: For drying solvents and creating products like catalysts and pigments.
- Agricultural: For producing animal feed, fertilizers, and pesticides.
- Biotechnology: For manufacturing recombinant proteins, vaccines, and other biopharmaceuticals.
- Environmental: For treating wastewater, solid waste, and air pollutants.
- Cosmetic: For creating powders and personal care products.
- Battery Materials: Emerging use in producing cathode and anode materials for lithium-ion batteries.
Disadvantages of Spray Drying
Despite its benefits, spray drying has some drawbacks:
- Limited Feed Viscosity: Typically handles feeds with viscosities below 500 centipoises, which may require dilution.
- High Capital Cost: Expensive to purchase and operate, with high energy consumption.
- Energy Intensive: Requires significant energy for heating the air and atomizing the feed.
- Operational Safety Concerns: Dry powders can be flammable or explosive, requiring robust safety measures.
Making Spray Drying Work for Your Business
To optimize the cost-benefit ratio of spray drying, it is crucial to choose the right equipment and suppliers. Recent innovations, such as high-speed rotary atomizers with magnetic bearing technology, offer greater efficiency and reduced maintenance costs, making spray drying a more viable option for many applications.
Conclusion
Spray drying has become a staple in many industries due to its advantages over other drying techniques. While it has its complexities and requires technical expertise, the benefits often outweigh the limitations. A thorough analysis of its advantages and disadvantages can help determine whether it suits your specific needs.
FAQs
- Alternatives to Spray Drying? Alternatives like ring dryers or roto flash dryers may be appropriate for certain applications.
- Temperature in Spray Drying? Typically, air heated to 200°C (about 400°F) is used to dry the atomized liquid.
- Spray Drying vs. Freeze Drying? Spray drying is generally more efficient for certain applications, as demonstrated by studies on solubility and moisture content.
- Unsuitable Products for Spray Drying? Products that are highly viscous, sensitive to heat, or reactive may not be ideal for spray drying.