Innovations in Powder Equipment Technology: Revolutionizing the Industry
Powder Equipment Technology
I. Introduction
The powder equipment industry has been on a remarkable journey of transformation in recent times. Technological innovations have become the driving force behind this evolution, reshaping the way powder equipment functions and its significance in various industrial arenas.
II. Key Innovations
A. Automation and Control Systems
Modern powder equipment is now equipped with intelligent sensors and programmable logic controllers (PLCs). These advanced components enable real-time and precise monitoring and adjustment of crucial parameters. For instance, in dryers, temperature, humidity, and airflow can be continuously regulated. This level of automation not only guarantees consistent product quality but also minimizes human error and optimizes energy efficiency. It further facilitates seamless integration into larger industrial production lines, streamlining the overall manufacturing process.
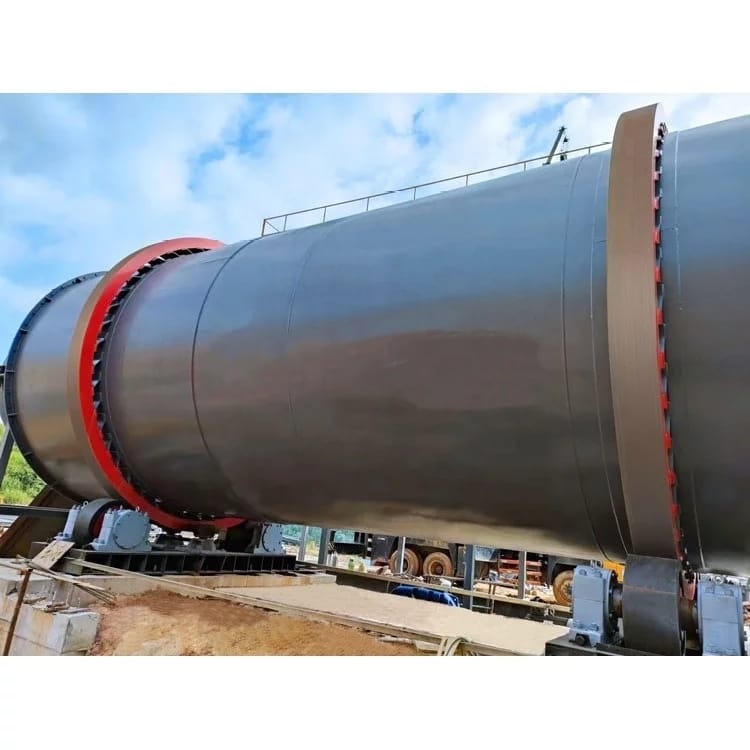
B. Advanced Materials
The development of high-strength, corrosion-resistant alloys and polymers has been a game-changer. These materials have extended the lifespan of powder equipment and expanded its application range. In crushers, specialized wear-resistant liners have reduced maintenance needs and downtime. They can withstand harsh operating conditions such as high temperatures, corrosive chemicals, and abrasive powders, making the equipment more reliable and cost-effective.
C. Nanotechnology
Nanotechnology has made a significant impact. By manipulating materials at the nanoscale, the surface properties of powders can be enhanced. This leads to powders with improved flowability, solubility, and reactivity. Nanocoatings on drying surfaces accelerate the drying process by enhancing heat transfer efficiency. In granulators, nanoparticles can modify the characteristics of granules, resulting in more uniform and stable products.
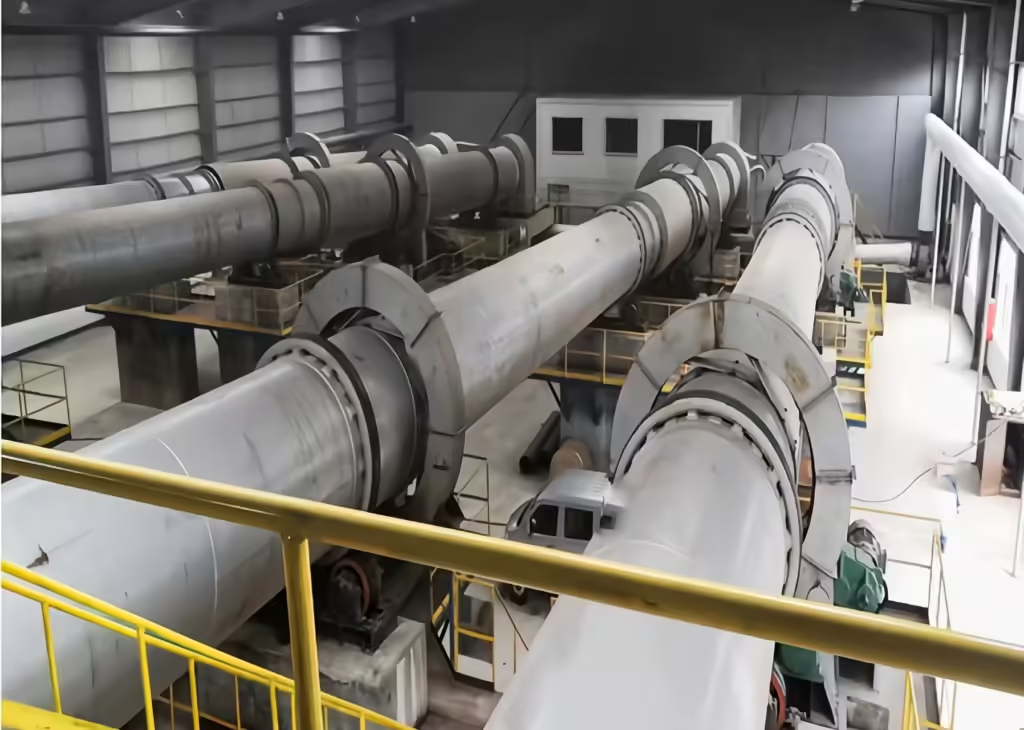
D. 3D Printing Technology
The emergence of 3D printing has opened new avenues for customization. It allows for the rapid prototyping and production of complex parts with optimized geometries. This means powder equipment can be tailored to specific industrial processes, maximizing performance and minimizing waste. For example, a mixer can be designed with a unique impeller shape for better mixing results.
III. Conclusion
The continuous stream of technological innovations in powder equipment technology is truly revolutionizing the industry. These advancements are leading to improvements in quality, efficiency, and sustainability, enabling manufacturers to meet the dynamic demands of modern industrial production. As technology progresses, we can look forward to even more ground-breaking developments that will redefine the powder equipment landscape.