How a Spray Dryer Works in Industrial Applications
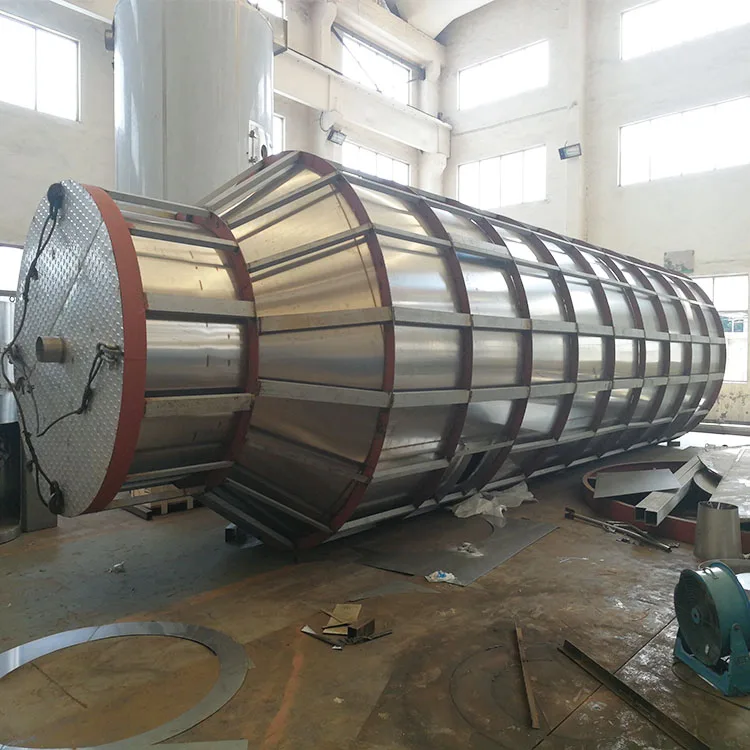
A spray dryer changes a liquid into a dry powder fast by spraying it into hot air. There are three main steps in this process. First, atomization splits the liquid into tiny drops. Next, hot air dries the drops and removes water quickly. Last, the finished powder is collected. This method helps you get good quality and work faster in your industry. You can change important settings like temperature, feed rate, and atomization pressure. This helps you make each product better and more stable. The table below shows how these settings affect your product’s quality and how well the process works.
Parameter | Effect on Product Quality and Efficiency |
---|---|
Inlet Temperature | Controls how fast water leaves and how big the powder is; the best range is 150-200°C for good drying and stable powder. |
Outlet Temperature | Decides how much water is left; 50-90°C makes sure the powder is dry enough but not damaged. |
Feed Rate | A higher feed rate makes more powder but can lower quality if the dryer cannot keep up; the best feed rate keeps drying steady. |
Atomization Pressure | Higher pressure makes smaller powder pieces, which helps them stay the same size and stable; usually between 1-5 bar. |
You can get the best results in your industry by learning how spray drying works and using the right settings on your spray dryer. When you use the spray dryer como funciona method, you make sure every product meets high quality rules for your industry.
Key Takeaways
Spray drying changes liquid into dry powder fast. It does this by breaking up the liquid. Then, it dries the small drops with hot air. After that, it collects the powder in a good way.
You can control things like temperature and feed rate. You can also change atomization pressure. This helps you make powders that are stable and high-quality. These powders fit what industries need.
Picking the right spray dryer parts is important. Using good collection methods helps too. This makes the product more pure. It also gives you more powder and keeps each batch the same.
Spray drying is used in food, medicine, and chemical factories. It saves time and energy. It also keeps sensitive ingredients safe.
Keeping the process steady is important. Cleaning the equipment often is needed. This keeps products safe and the same every time. It also stops energy from being wasted.
Spray Dryer Working Principle
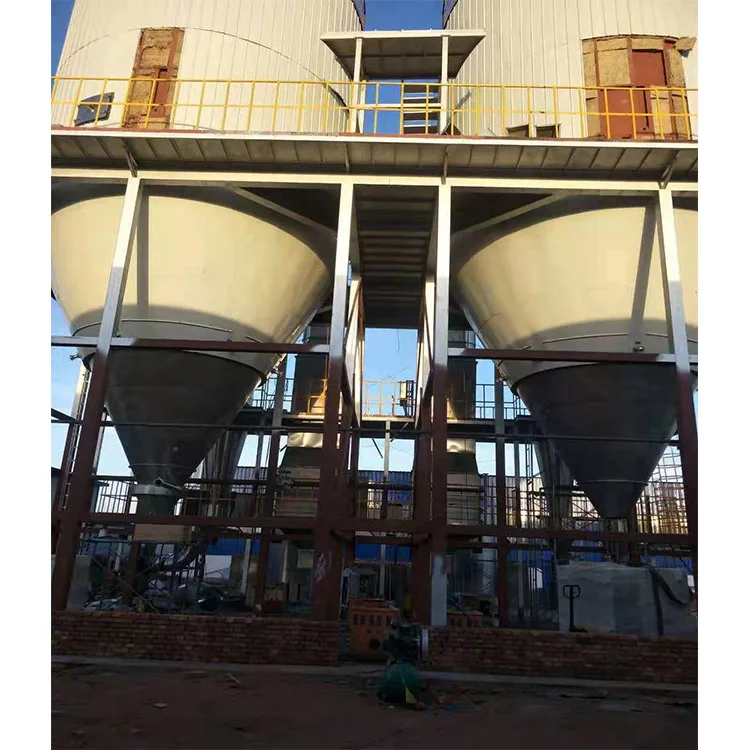
The spray dryer working principle helps turn liquid feed into dry powder fast. Many industries use this process to make sure products are high quality. There are three main steps: atomization, drying with hot air, and collecting particles. Each step is important for the final product and how it works.
Atomization Process
First, the liquid feed breaks into tiny droplets. This is called atomization. Different atomizers can be used, like pressure nozzles, two-fluid nozzles, or rotary atomizers. Rotary atomizers spin very fast to make a thin film of liquid. The film stretches and breaks into small droplets. If you spin faster, you get even smaller droplets. Smaller droplets dry faster because they have more surface area. The size and sameness of the droplets change the final powder size and quality. In factories, people pick the atomizer type based on what they want to make.
Rotary atomizers spin fast to make small droplets.
Pressure nozzles push liquid through a small hole to make droplets.
Two-fluid nozzles use air or steam to break up the liquid.
You can change the droplet size by changing the atomizer speed, pressure, or feed rate. This helps you control the powder size and quality.
Drying with Hot Air
After atomization, the droplets go into a chamber with hot air. The air is usually between 100°C and 300°C, depending on what you are making. Droplets dry quickly because they have a lot of surface area. Water leaves the droplets almost right away, turning them into solid particles. Fast drying keeps the product good and stops heat damage. You can change the air temperature and how fast it moves to fit your product. Higher temperatures and faster air can dry things quicker, but you need to be careful not to hurt sensitive products.
Tip: To save energy, you can change the air temperature, flow, and feed concentration. Lower feed concentration and changing the air flow can help save energy and keep the product good.
The drying chamber’s design also matters. A good chamber spreads hot air and droplets evenly. This makes the powder even and keeps the quality the same.
Particle Collection
When the droplets dry, you need to collect the solid particles. You can use cyclone separators, bag filters, or electrostatic precipitators. Cyclone separators spin the air to pull out the dry particles. Bag filters and electrostatic systems catch even the smallest pieces, so you do not lose product. How you collect the powder changes the purity, amount, and quality of your product. In factories, people want to get as much product as they can and keep the process clean.
Collection Method | How It Works | Effect on Product Quality and Yield |
---|---|---|
Cyclone Separator | Spins air to separate particles by weight | Good for most particles, high yield |
Bag Filter | Traps fine particles in filter bags | Improves purity, catches small product |
Electrostatic Precipitator | Uses electric charge to collect fine particles | Best for very fine product, high purity |
You can pick the best way to collect powder based on what you are making. Good collection systems help you meet rules and give you the same product every time.
If you know how each spray dryer step works, you can control the powder’s size, shape, and quality. This helps you make products that meet industry needs and stand out for their quality.
Spray Dryer Como Funciona
Key Components
When you want to understand spray dryer como funciona, you need to know the main parts that make the process work. Each part helps you turn liquid into a dry product with the right quality. Here are the key components you will find in a spray dryer como funciona system:
Feed System: This part moves your liquid to the atomizer. You control the flow to match your product needs.
Atomizer: The atomizer breaks your liquid into tiny drops. You can use a pressure nozzle, rotary atomizer, or two-fluid nozzle. The type you pick changes your product’s size and shape.
Drying Chamber: This is where hot air meets the droplets. The chamber can be cylindrical, conical, or rectangular. The shape helps you collect your product and keep it even.
Air Heating System: This system heats the air or gas. Hot air dries your product fast and keeps it safe.
Cyclone Separator: This part spins the air to pull out your dry product. You get more product and less waste.
Bag Filter or Scrubber: These catch fine particles. You keep your product pure and the air clean.
Powder Collection: This is where you gather your finished product. Good collection means you do not lose any product.
Note: Picking the right components helps you get a stable, high-quality product every time you use spray dryer como funciona.
Component | Description |
---|---|
Feed System | |
Atomizer | Converts fluid into small droplets; types include high pressure and rotary nozzles. |
Drying Chamber | Heated chamber where water evaporates from droplets, leaving powder. |
Air Heating System | Supplies hot air or gas to dry droplets. |
Cyclone Separator | Uses rotational airflow to separate and collect powder from air stream. |
Bag Filter or Scrubber | Removes fine particulates from drying air. |
Powder Collection | Extracts powder from air stream, directing product to collection points. |
Operation Steps
You can follow clear steps to see how spray dryer como funciona in practice. Each step helps you move from liquid to a dry product that meets your needs.
Formulation Screening and Definition
You start by picking the right mix for your product. This step helps you decide what goes into your spray dryer como funciona process.Identification of Process Constraints
You look at what limits your process. You check things like temperature, air flow, and how fast you feed the liquid. This keeps your product safe and stable.Definition of Thermodynamic Design Space
You set the best range for drying. You pick the right heat and air settings for your product. This step helps you avoid damage and get the best product.Verification Through Spray-Drying Experiments
You test your settings. You run the spray dryer como funciona and check if your product meets your goals. If not, you change the settings and try again.
Tip: Always check your product at each step. This helps you catch problems early and keep your product quality high.
You can see that spray dryer como funciona gives you control at every stage. You can change each step to fit your product. This method helps you make a product that is dry, stable, and ready for use or sale.
Industrial Applications
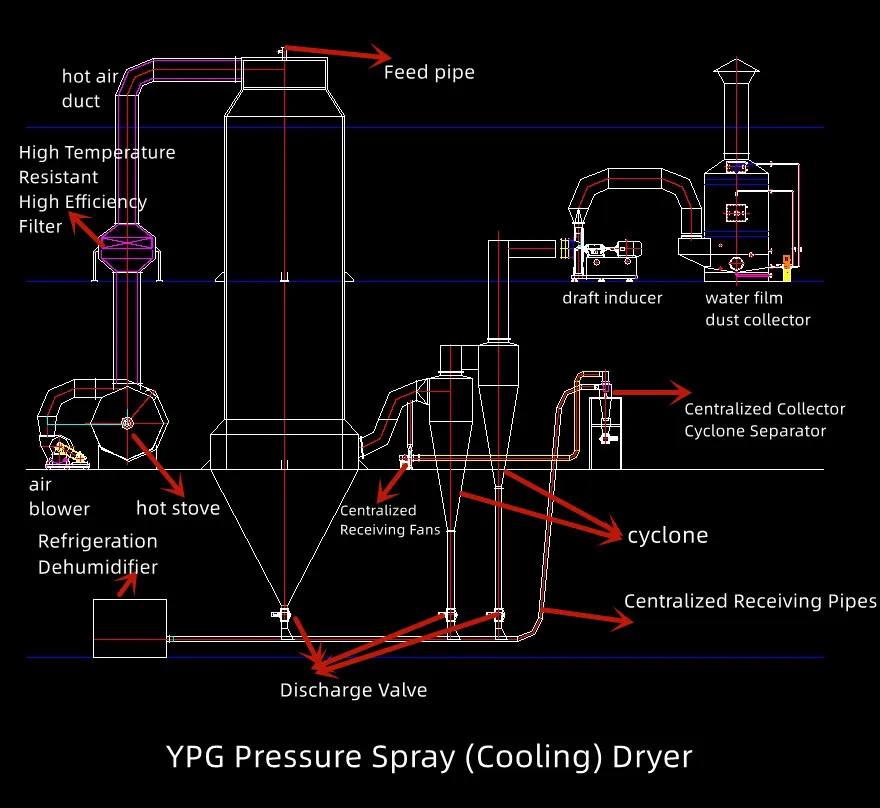
Spray dryer applications are important in many industries. This technology changes how products are made in food, pharmaceutical, and chemical industries. The table below shows how regions use spray drying and what helps each area grow.
Region | Market Share (2024) | CAGR Forecast (to 2033) | Key Drivers and Notes |
---|---|---|---|
Asia-Pacific | ~38% (USD 2.6B) | 8.5% | Rapid industrialization, food processing, pharmaceuticals, rising consumer demand |
North America | ~32% | Steady growth | Established industries, technological innovation, process optimization |
Europe | ~24% | Steady growth | Stringent quality and environmental regulations, sustainability focus |
Latin America & MEA | ~6% | Emerging market | Growing demand for processed foods and pharmaceuticals, infrastructure investments, regulatory challenges |
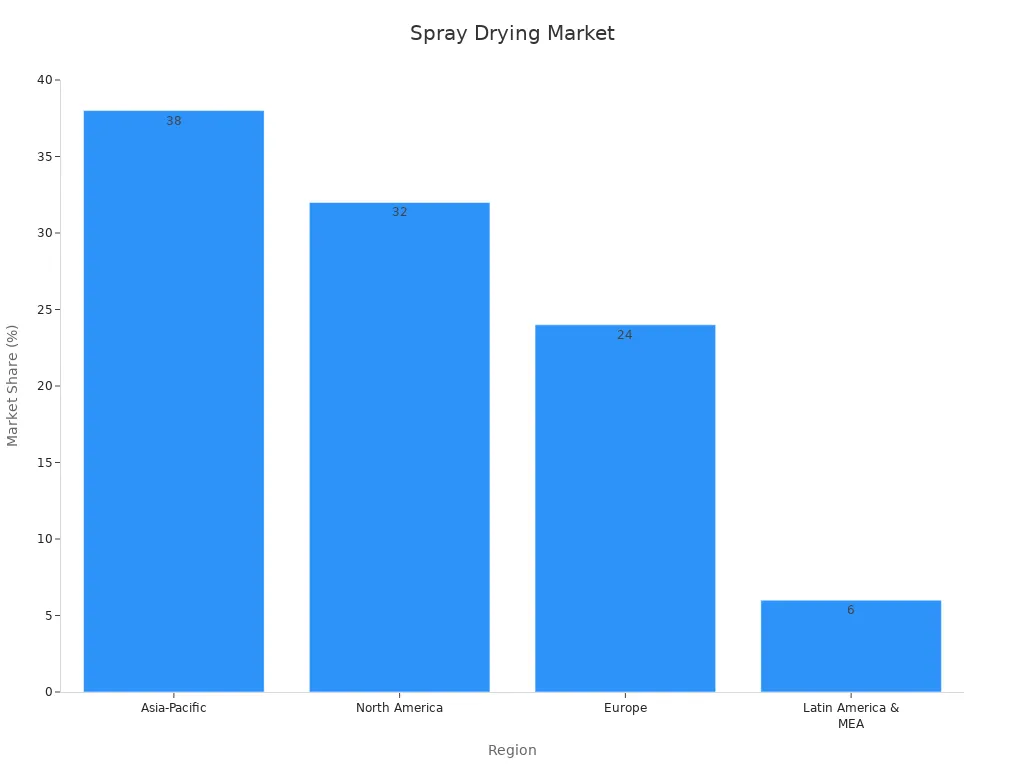
Food and Beverage
Spray dryers help the food industry make products that are easy to store and use. You can turn liquids like milk, coffee, and juice into powder. This is good for instant drinks and plant-based foods. Spray drying keeps more healthy parts in the food than freeze drying. It also gives you more powder and better results in the body. The food industry likes spray drying because it is fast and can handle big batches. This makes food processing work better.
Pharmaceuticals
The pharmaceutical industry uses spray dryers to make powders with the right size and stability. This is important for drugs you breathe in, antibiotics, and biologics. Powders dissolve fast and deliver medicine where it is needed. Spray drying helps make products quickly and in large amounts. You can go from lab to factory without losing quality. Reports show the pharmaceutical industry is growing fast with spray drying. More companies are buying new spray dryers and using more machines. Spray drying is trusted for safe and clean production.
Chemicals
Spray dryers are used in the chemical industry to make powders like catalysts and pigments. This helps make powders that are all the same size and not too wet. Spray drying makes products safer and easier to use. It also saves time and energy compared to freeze drying. The chemical industry likes spray drying because it works for both heat-sensitive and strong materials. You can use special plans to get the best results and waste less. Spray drying helps meet strict rules and makes work more efficient.
Benefits and Product Quality
Efficiency
Spray drying works fast and saves energy. It dries products quicker than freeze-drying. Modern spray dryers help lower costs and help the environment. You can set the temperature, airflow, and feed rate. This helps you get more product in less time. Protective agents like trehalose and L-isoleucine keep sensitive things safe. These agents also stop moisture from hurting your product. This keeps the quality high.
Here is a table that shows how good settings make spray drying better and improve product quality:
Parameter/Property | Optimized Value / Result |
---|---|
Inlet Air Temperature (IAT) | 160 °C |
Carrier Agent Concentration | Maltodextrin 14%, Gum Arabic 6% |
Feed Flow Rate (FFR) | 350 rpm |
Feed Total Soluble Solids | 15 °Brix |
Moisture Content | 2.91% |
Dispersibility | 92.50% |
Water Solubility Index (WSI) | 94.17% |
Flowability | 25.83° (angle of repose) |
Sensory Evaluation | 25% w/v reconstitution concentration preferred |
These numbers show the product is easy to use and dissolves well. This is a big reason why spray dryers are helpful.
Consistency
Spray drying gives the same results every time. You can keep temperature, airflow, and feed rate steady. This means each batch has the same particle size and moisture. The spray dryer can handle small changes in the liquid feed. This helps keep each batch almost the same. It also helps with quality checks.
You get the same particle size, so your product mixes well.
Even particles stop clumps and keep the product stable in storage.
You can change atomization settings to fit your needs and keep quality high.
Note: Having the same particle size and moisture helps your product work better.
Product Quality
Spray drying keeps your product safe and high quality. It protects nutrients and active parts. For example, maltodextrin can cover sensitive ingredients. This keeps them safe from heat and air. You can keep omega-3 fatty acids and other nutrients by setting the right air temperature and pump speed.
Quality Metric | Range/Value | Significance for Product Preservation |
---|---|---|
81.57% to 89.30% | Protects core materials from oxidation and degradation | |
EPA Retention | 1.87 to 2.19 g/100 g | Confirms nutritional quality preservation |
DHA Retention | 2.75 to 3.20 g/100 g | Validates preservation of key nutrients |
Percent Loss of EPA/DHA | 2% to 18% | Shows minimal thermal degradation |
Peroxide Value (PV) | Controlled by IAT | Maintains oxidative stability |
Particle size is important for keeping your product stable and easy to use. Even particle size helps with mixing and flow. Spray drying lets you change settings to get the best quality. This helps many industries, especially those with heat-sensitive products.
Challenges
Energy Use
Spray dryers use a lot of energy. They need heat to dry the liquid. In food, chemical, and ceramics factories, spray dryers use between 3 and 20 GJ for each ton of water removed. Most dryers use about 4.87 GJ per ton. This makes energy a big cost for making food or chemicals. About 29% of the energy is wasted compared to the best dryers. You can save energy by using heat recovery systems. Air-to-air heat exchangers help you reuse heat and save money. Closed-loop systems also use less power and save nitrogen. This is important for some chemical products. You can also use solar heaters or combined heat and power systems to make your process better.
Parameter | Value/Range | Notes |
---|---|---|
Specific energy consumption (E_s) | 3–20 GJ/t water | Range for spray dryers in food, chemical, and ceramics industries |
Average specific energy consumption | 4.87 GJ/t water | Typical value across surveyed dryers |
Estimated energy wastage | ~29% | Compared to ideal adiabatic dryer |
Tip: You can save energy by changing air flow and using heat recovery. This helps you make your product with less waste.
Equipment Choice
Picking the right spray dryer is important for your product and costs. You need to think about safety, energy use, and cleaning. For chemical products, check if the dryer’s materials match your product. This stops contamination. Look at airflow, atomizer type, and chamber shape. These things change your product’s size and shape. Some products need special features like inert gas flushing to keep out oxygen. Think about the total cost, including fixing and energy. If your product is heat-sensitive, choose a dryer with good temperature control. Ask experts for help if you are not sure what to pick.
Safety features like explosion and fire protection are important for chemicals.
Atomizer and nozzle design change your product’s particle size and sameness.
Good maintenance and cleaning keep your product safe and your process working.
Consistency
You want every batch to be the same. Consistency is very important in spray drying. You must control feed concentration, inlet air temperature, and atomization pressure. These settings change your product’s size, moisture, and surface. Good quality control uses experiments to find the best settings. You can use Plackett-Burman or Box-Behnken designs to test what matters most. If you keep your process in the right range, your product will dissolve well and stay stable. This works for both food and chemical products. Sensors and smart controls help you watch your process in real time. This lets you fix problems early and keep your product quality high.
Quality Control Aspect | Description |
---|---|
Critical Process Parameters | Feed concentration, inlet air temperature, atomization pressure |
Impact on Product Quality | Affects particle size, moisture, surface area, and stability |
Outcome | Consistent product quality and performance |
Note: Keeping your process steady helps you give your customers the same good product every time.
If you learn the three main steps—atomization, drying, and collection—you can get good at spray drying. Each part, like the atomizer and powder collector, is important for making a quality product.
Spray dryers let you make powders that are always the same and work well.
You can change the settings to match what you need and get better results.
Are you thinking about using spray drying for your business? Ask an expert to help you pick the best way for your products.
FAQ
What products can you make with a spray dryer?
You can make milk powder, instant coffee, egg powder, flavors, vitamins, and chemicals. Spray dryers help you turn many liquids into dry powders for food, medicine, and industry.
How do you clean a spray dryer?
You should clean the spray dryer after each batch. Use water or cleaning agents to wash the chamber, atomizer, and collection system. This keeps your product safe and prevents mixing of different batches.
Why does spray drying work well for heat-sensitive products?
Spray drying uses fast drying at controlled temperatures. The droplets dry quickly, so heat-sensitive ingredients do not get damaged. You keep more nutrients and active parts in your product.
How do you control the size of the powder particles?
You can change the atomizer speed, pressure, and feed rate. Higher speed or pressure makes smaller particles. Lower speed or pressure makes bigger particles. This helps you get the right powder size for your needs.