Evaluación de métodos experimentales y computacionales en cálculos de diseño de secador de spray
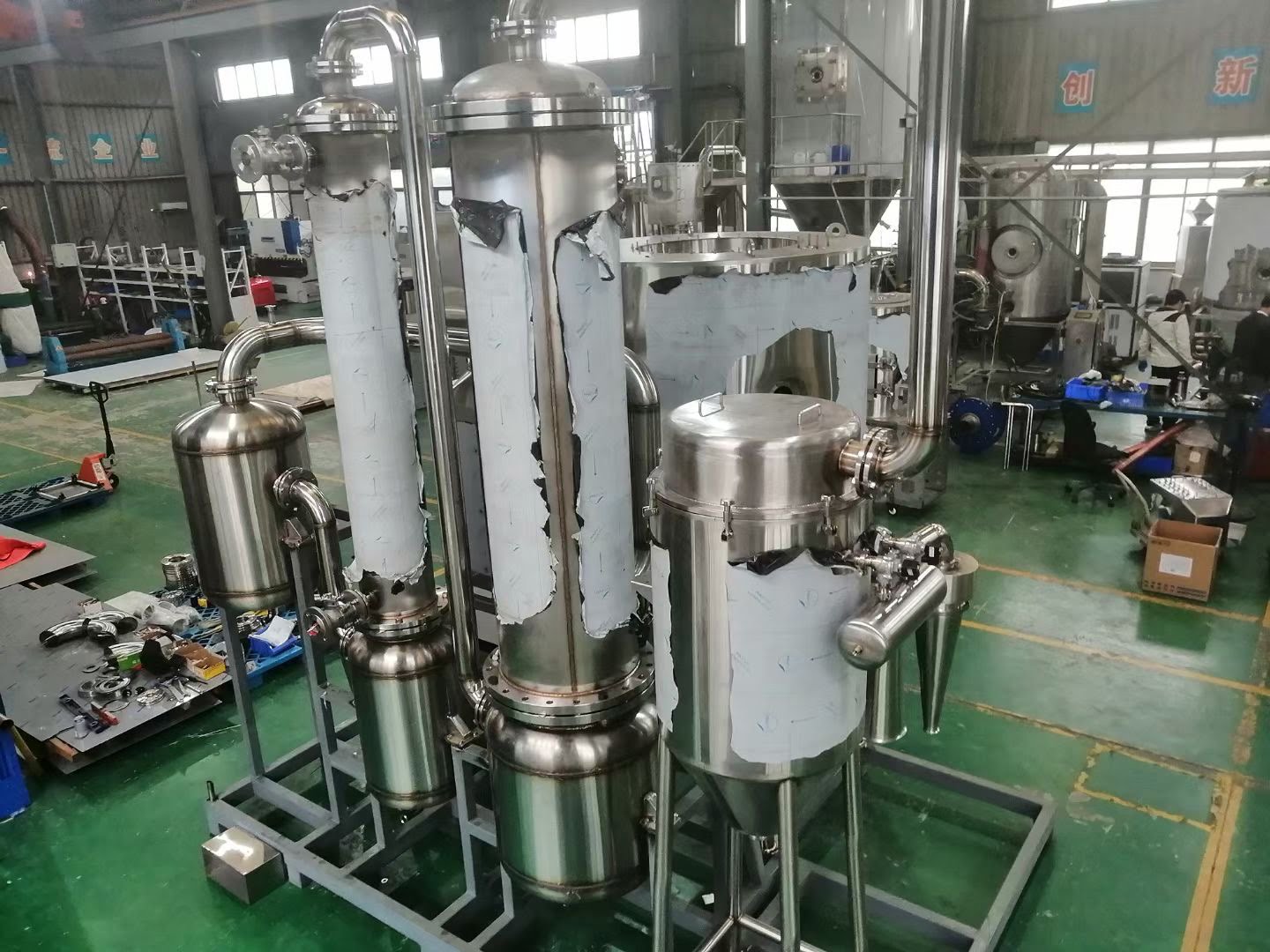
Choosing the right way to do spray dryer design calculations is important. It affects how well the process works and how good the product is. Scientists use experiments, like statistical design of experiments, to find out how process changes affect the product.
Model-based ways use mass and energy balances. These help lower the number of experiments needed. They also make it easier to use the method on a bigger scale.
Only using statistical methods might not be as exact. This is a bigger problem when making more product at once.
Process Parameter | Control Strategy / Range | Impacto en la calidad del producto / Eficiencia |
---|---|---|
Drying-gas outlet temperature | Product temperature 5–20 °C lower than outlet | Strong link to product characteristics |
Droplet size control | Managed by atomization energy | Uniform drying, consistent product morphology |
Picking the best method makes spray dryer design calculations more trustworthy and repeatable.
Control de llave
Experimental methods give real data. This data shows how spray dryers work. It also helps make products better.
Computational models like CFD and thermodynamic models help engineers test ideas fast. These models save time and resources.
Using both experimental data and computational models gives better spray dryer designs. These designs are more accurate, reliable, and easy to scale.
Picking the best method depends on project goals. It also depends on what you have and what the product needs. This helps make drying work well and not cost too much.
In the future, AI, digital twins, and energy-saving tools will help spray drying. These trends will make it smarter, greener, and more efficient.
Scope and Criteria
Main Methods Overview
Spray dryer design calculations use two main types of methods. These are experimental and computational methods. Experimental methods use real measurements to see how things change during drying. Scientists use small spray dryers in labs for these tests. They use tools like Pitot anemometers and pressure switches. These tools check how fast the drying gas moves and how much gas flows. They also measure atomization gas pressure. The information from these tools helps scientists understand the drying process better.
Computational methods use things like thermodynamic models, CFD, Lagrangian particle tracking, y energy or exergy analysis. Thermodynamic models use mass and energy balances to guess what will happen, like the outlet temperature. CFD shows detailed pictures of temperature and speed inside the dryer. Lagrangian methods follow each droplet. Energy and exergy analysis look at how efficient the process is and how much entropy is made. Studies show that using these methods with machine learning can make results better and cut down on extra experiments. Scientists often check if their models are right by comparing them to real test data.
Nota: Each method has its own strengths. Experimental methods give direct proof, while computational models let you test many ideas quickly and help improve the process.
Evaluation Metrics
Experts use different ways to compare methods for spray dryer design calculations:
Accuracy: People use things like Root Mean Square Error (RMSE), Mean Absolute Error (MAE), and Coefficient of Determination (R²) to see how close model guesses are to real results. Por ejemplo, RMSE for outlet temperature can be between 2.15 K and 14.91 K. R² values can go as high as 0.99.
Practicality: It is important to know how easy a method is to use. CFD takes a lot of time and computer power. Thermodynamic models are faster and need less data.
Scalability: A good method should work for both small lab tests and big factories. The idea of design space helps control the process and make it bigger.
Validation: Good methods must match what happens in real life. Scientists use pilot tests and factory data to check if their models are correct.
These points help engineers pick the best way for their needs.
Experimental Methods
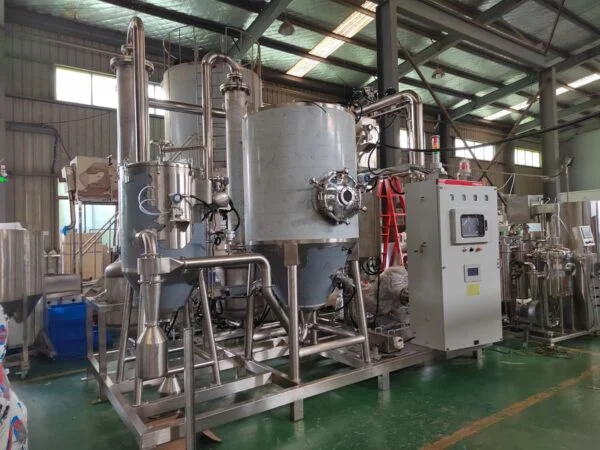
Residence Time Distribution
Engineers use residence time distribution, or RTD, to see how long particles and gases stay in a spray dryer. RTD helps them know how changes in design affect drying and product quality. Researchers often use dye pulse injection to follow particles as they move. They match the data to models like CSTR-TIS for better understanding.
Spray Dryer Design | Particle-to-Gas Mean Residence Time Ratio (s/s) | Spread of RTD (n) | Key Observations |
---|---|---|---|
Design 1 & 2 | 13–18 | Higher particle residence times; more wall deposition | |
Design 3 & 4 | 1.5–2.5 (3), 1.0–1.7 (4) | 5–8 | Lower ratios; improved performance; less wall deposition |
Newer designs with conical chambers work better. They lower wall build-up and make RTD spread wider. This helps with recirculation and drying. RTD tests also show that CFD models are correct.
Physical Measurements
Physical measurements are very important in experimental methods for spray dryer design. Scientists measure things like temperature, humidity, and leftover moisture right from the dryer. They use tools such as thermocouples, humidity sensors, and pressure switches. These numbers help them make models that show what happens in the dryer. Por ejemplo, a dynamic model of a four-stage spray dryer used good test data to find important numbers. The model’s guesses for temperature and moisture were close to real test results. Lab data on moisture and glass transition temperature made the model even better.
Consejo: Good physical measurements help engineers change settings and make products more consistent.
Validation with Industrial Data
Checking with industrial data makes sure experimental methods work in real life. Tests with pilot spray dryers and fumed silica showed measured particle sizes matched model guesses. Lab fluidized bed tests helped set drying numbers, like heat and mass transfer, to fit temperature and moisture data. These numbers helped make good simulations and designs for big dryers. Studies also checked model guesses with data from real dryers making food. The models guessed feed flow, outlet temperature, tamaño de partícula, and drying speed very well. This strong match shows experimental methods help make spray dryer design calculations reliable and help improve processes for many products.
Computational Methods
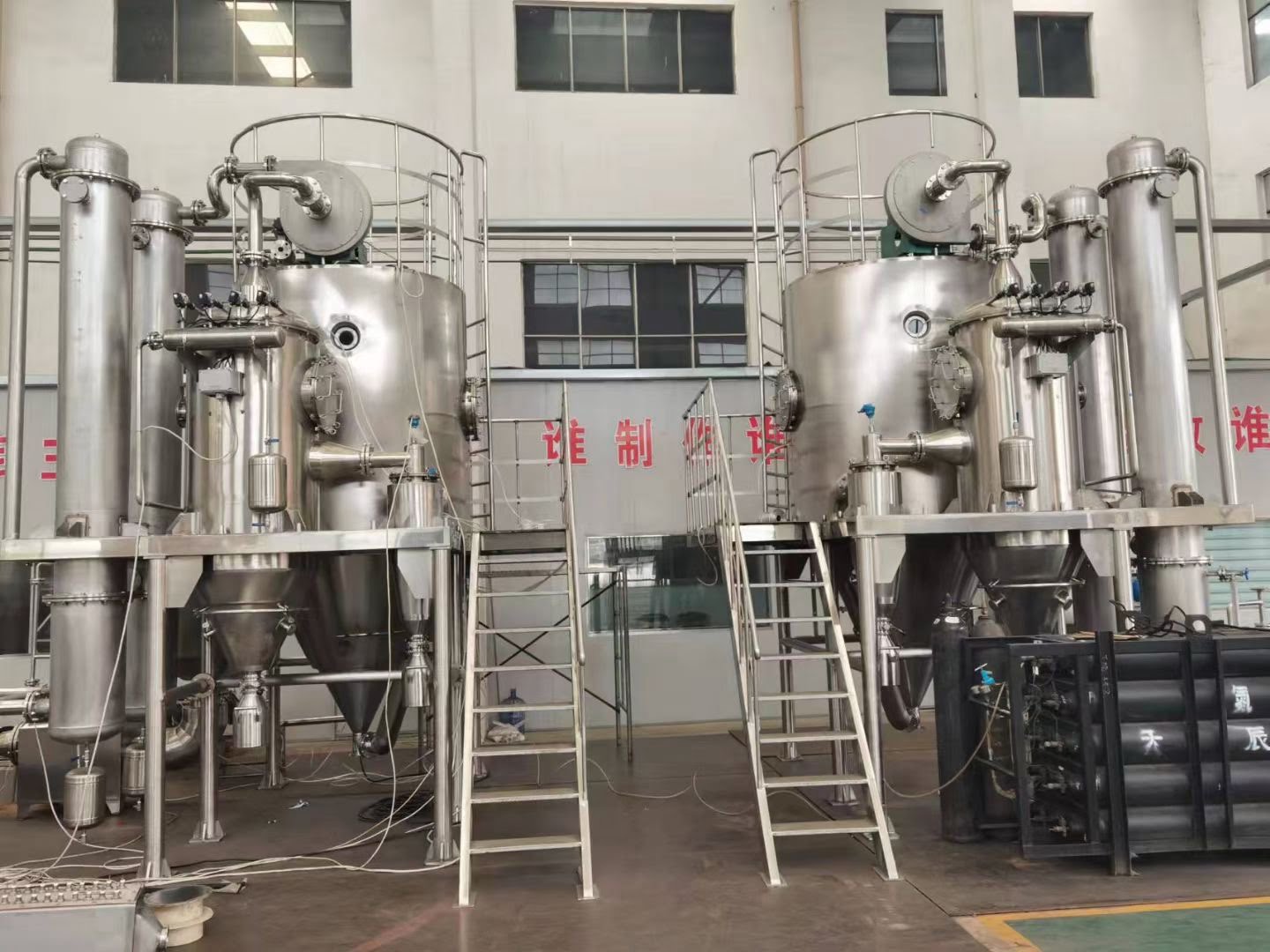
Thermodynamic Models
Thermodynamic models help engineers guess how heat and mass move in a secador por aspersión. These models use numbers like air temperature, humidity, and how fast air moves. Engineers often use well-known rules for heat transfer and pressure drop, like the ones from Kays and London. They also use test data about fouling, which means milk powder can stick to heat exchangers. This sticking changes how heat moves and how much energy the dryer needs.
Engineers use these models to see how design changes affect how the dryer works.
They can guess how much energy the dryer will use and how much product it will make.
Thermodynamic models also help decide if a new design will save money.
A real example with a milk spray dryer showed these models can guess real results. The models used real numbers, like exhaust air temperature and humidity, to match what happened in the factory. This makes thermodynamic models a trusted tool for spray dryer design calculations.
CFD and Lagrangian Approaches
Computational Fluid Dynamics, or CFD, and Lagrangian methods show what happens inside a spray dryer in detail. CFD models use math to show how air and particles move. Lagrangian tracking follows each droplet as it dries.
Engineers use Eulerian–Lagrangian frameworks to model two-phase flow.
They solve Navier–Stokes equations for air and track heat and mass transfer for droplets.
Models can show how long particles stay in the chamber, which matters for heat-sensitive products.
CFD predicts gas flow, drying rates, and where particles land inside the dryer.
CFD models have matched test data well. Por ejemplo, models guessed how changing wall conditions, like insulation or cooling, changed drying and powder recovery. Two-way coupling between heat and mass transfer made the models better. CFD also lets engineers try new designs without building expensive test dryers.
Energy and Exergy Analysis
Energy and exergy analysis help engineers find where a spray dryer wastes energy. Energy analysis shows how much power the dryer uses. Exergy analysis goes further by showing where energy is wasted and how to fix it.
Engineers use these methods to compare different dryer designs.
Exergy analysis points out which parts of the dryer waste the most energy.
Improvements like better insulation or using solar heaters can lower energy use.
Parámetro | Valor | Descripción |
---|---|---|
0.768 kilovatios | Power from electrical source | |
Solar air heater power consumption | 0.327 kilovatios | Power from solar source |
Heat loss reduction by polystyrene sheets | 4.9→2.27 W·m⁻²·K⁻¹ | Insulation improvement |
Reduction in electrical energy input ratio | 2.68→1.69 | 30% solar energy contribution |
Max exergy improvement in condenser | 0.233 kilovatios | Highest exergy destruction |
Exergy improvement in drying chamber | 0.294 kilovatios | Significant inefficiency |
Exergy improvement in electric heater | 0.152 kilovatios | Room for efficiency gain |
Exergy improvement in solar air heater | 0.097 kilovatios | Potential gains in solar preheating |
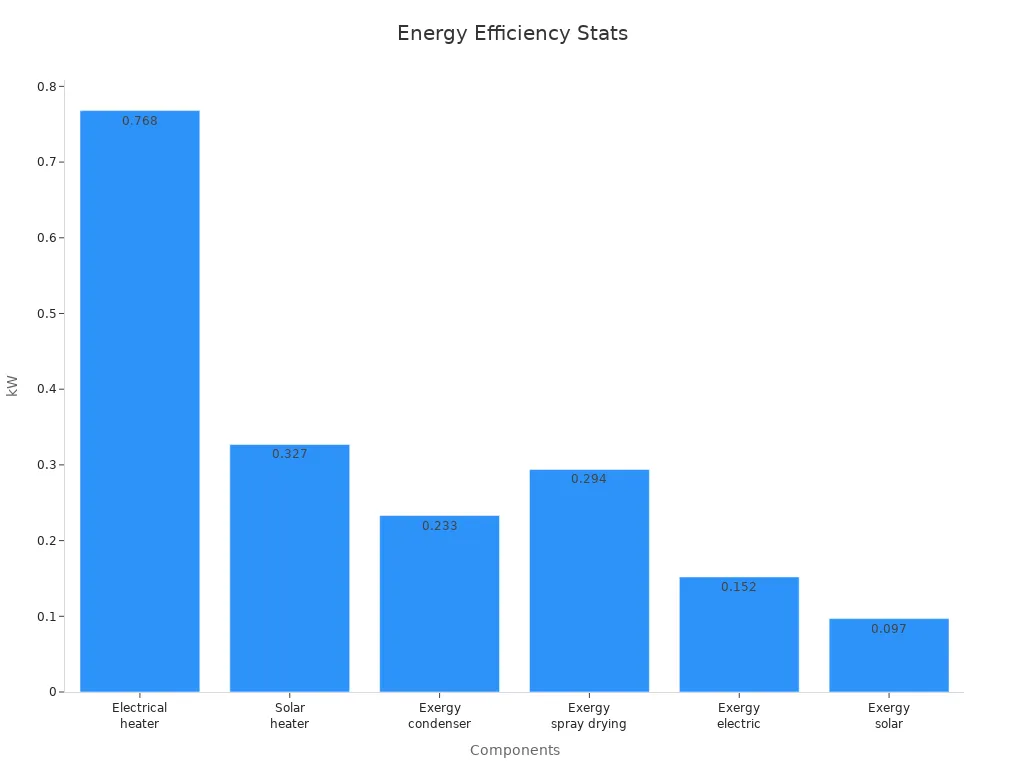
Exergy analysis gives clear ideas for making spray dryers work better. This method helps engineers make good design choices and save energy in real factories.
Comparing Spray Dryer Design Calculations
Accuracy and Reliability
Engineers need accuracy and reliability when picking methods for spray dryer design calculations. Experimental methods give direct measurements. These help check if models are correct and make results trustworthy. Computational models, like CFD and thermodynamic models, guess important things such as outlet temperature, droplet size, and product yield. These models often match real test data well. Por ejemplo, in making medicine, a data-driven model predicted particle size with high accuracy. Almost all errors were less than 2.5 micrometers, which is under 10% of the allowed range. This means the model can take the place of lab tests and help with real-time checks. Engineers can trust these models to include important things like spray nozzle type, feed viscosity, and density. This makes them good for both small and big projects.
Nota: Good models mean fewer experiments and faster design work.
Resource Needs
Resource needs are important when choosing a method for spray dryer design calculations. Experimental methods need equipment, materials, and time to set up and collect data. Por ejemplo, a study used a Büchi Mini Spray-dryer with a feed rate of 2 mL/min and an aspiration rate of 35 m³/h. Yield was found by weighing the dry powder and comparing it to the dry material put in. These details help engineers plan for bigger production.
The table below shows common resource needs for spray drying:
Resource Category | Data / Values |
---|---|
Capacidad de producción | Pilot-scale: 1-5 kg/hr water evaporation |
Small production: 5-50 kg/hr water evaporation | |
Medium production: 50-250 kg/hr water evaporation | |
Large industrial: 250-4,000+ kg/hr water evaporation | |
Energy Consumption | Usually 1.2-1.7 kWh for each kg of water evaporated |
Feed Properties | Viscosity up to 300 cP |
Solids content 1-50% | |
Operational Timeline | Engineering and design: 2-3 months |
Equipment fabrication: 3-8 months | |
Instalación: 1-2 months | |
Commissioning and validation: 1-3 months | |
Production ramp-up: 1-2 months | |
Maintenance Requirements | Yearly maintenance cost: 3-5% of starting cost |
Atomizers: 500-1000 hours, air filters: monthly | |
Gaskets and seals: every three months, control checks: twice a year |
Computational methods, like CFD, need strong computers and special software. But they use less physical stuff and can make the design process faster. Engineers must think about these needs and match them to their goals and budget.
Scalability
Scalability shows if a method works for both small labs and big factories. Engineers test this by checking model guesses and real results at different sizes.
Spray drying was done from 5 grams to 400 grams using three machines: Buchi B-290, Procept 4M8Trix, and FluidAir. This showed the process worked well for different batch sizes.
Tests showed acetone left in the product was under 1%, proving good drying at all sizes.
Product yield went up from 21% to over 60% after changing inlet temperature and machine settings.
Mechanistic and CFD models guessed droplet size, drying speed, outlet temperature, and yield. These guesses matched real data well (R² > 0.80).
Cyclone separation worked for particles bigger than 18 micrometers, with high collection using good cyclones.
CFD models helped show how gas and droplets moved in bigger dryers. This helped engineers fix problems like particle breakage and clumping.
Changing drying gas flow, inlet temperature, and feed flow based on model guesses lowered wall build-up and made scaling up easier.
In big medicine factories, models predicted particle size (dv50) very well. Almost all errors were less than 2.5 micrometers, which is under 10% of the allowed range. This proves advanced models can help with big production and real-time quality checks. Engineers can use these methods to design and improve spray dryers for many uses.
Recommendations
Method Selection
Picking the right method for spray dryer design depends on what you want to make, what you have, and what your product needs. Engineers can use a step-by-step plan to choose well.
Start with small spray-drying tests. This helps pick polymers and drug amounts while using less material.
Do not use old ways like solvent casting. These do not copy real spray-drying and can give wrong results.
Use lab spray-drying in every step of making the product. This makes guesses better and cuts out extra steps.
Try a three-step plan. This can use 13 times less material and take 12 times less time than old ways.
Check if small batches are like big ones. Things like mixing and glass transition temperature stay the same, so you can change things early.
Use common lab tools like mDSC, XRPD, and PLM. Most labs have these, and they work for many projects.
Pick a method that fits your limits. Think about how much material you have, how much time you need, and what you want your product to be like.
Consejo: Engineers should also look at energy use, how much they can make, and how long machines last. Por ejemplo, picking a spray dryer that is 30% bigger can help if you want to make more later. Material things like feed viscosity and how it handles heat help you choose the right atomizer and chamber. Money matters too, like how much the machine costs and how long it takes to pay off.
Combining Approaches
Using both experimental and computational methods together often works best for spray dryer design. Engineers use both to check models, make better designs, and guess product features.
CFD simulations and test data together can show where particles stick or clump. This helps find the best nozzle and makes the product more even.
Test results, like droplet size and drying, help make sure math models are right. These models then guess how changes affect particle size, density, and moisture.
Using simple and detailed models lets engineers study hard things like wall build-up. Test data on outlet temperature and moisture help check these models.
Putting computer guesses and real results together helps make better designs, scale up, and run spray dryers.
Nota: Using both ways helps engineers make better choices, control the process, and avoid mistakes when making more product.
Future Trends
Spray dryer design keeps changing as new tech and ideas come out. Some trends are shaping what comes next.
AI and machine learning help control the process and fix problems before they happen. These tools can cut surprise stops by up to 45%.
Digital twins make development 30-40% faster. They help with design and running tests.
Heat recovery systems can save 25-35% of energy, making spray drying use less power.
Closed water loops can cut water use by up to 90%, which is good for the planet.
Smaller and modular machines save 40-60% of space and make it easy to add more later.
New materials, like special alloys, help machines last 40-50% longer.
Hybrid tech, like ultrasonic spray drying, uses 15-20% less energy and makes better products.
Special ideas, like aseptic and nano-spray drying, help with medicine and food.
Money facts show most new systems pay for themselves in 2-4 years because they cost less and make better products.
The future will have smart, closed-loop, and blockchain systems. These will make spray drying greener and smarter.
Engineers should keep learning about these trends to stay ahead and make sure their spray dryer design is up to date.
Engineers see that using experimental and computational methods helps spray dryer design. Experimental data proves if the results are correct. Computational models let engineers try new ideas quickly. Teams should pick a method that fits their project and what they have. Using both ways together often gives better results. In the future, research may look at smarter controls and saving more energy.
Preguntas más frecuentes
What is the main difference between experimental and computational methods?
Experimental methods use real measurements from lab or pilot secadoras. Computational methods use math models and computer programs to guess results. Both ways help engineers make better spray dryers, but each has its own strengths.
Why do engineers combine experimental and computational approaches?
Engineers use both to get more accurate answers. Experimental data checks if models are correct. Computer tools let them try many ideas fast. Using both helps make better designs and fewer errors.
How does CFD help in spray dryer design?
CFD, or Computational Fluid Dynamics, shows how air and droplets move inside the dryer. Engineers use CFD to spot problems, test new ideas, and make products better without building lots of test dryers.
What factors affect the choice of design method?
Engineers think about project goals, what they have, what the product needs, and how much time they have. They also look at energy use, equipment size, and cost. The best method depends on these things.
Can spray dryer models predict product quality?
Sí. Many models can guess important things like particle size, humedad, and yield. Engineers use these guesses to control quality and make the drying process better.