Estudios de caso: Cómo el equipo de polvo está transformando la industria química
Powder Equipment is Transforming the Chemical Industry
The chemical industry is constantly evolving, and powder equipment has emerged as a key enabler of transformation, improving production processes, product quality, and overall efficiency.
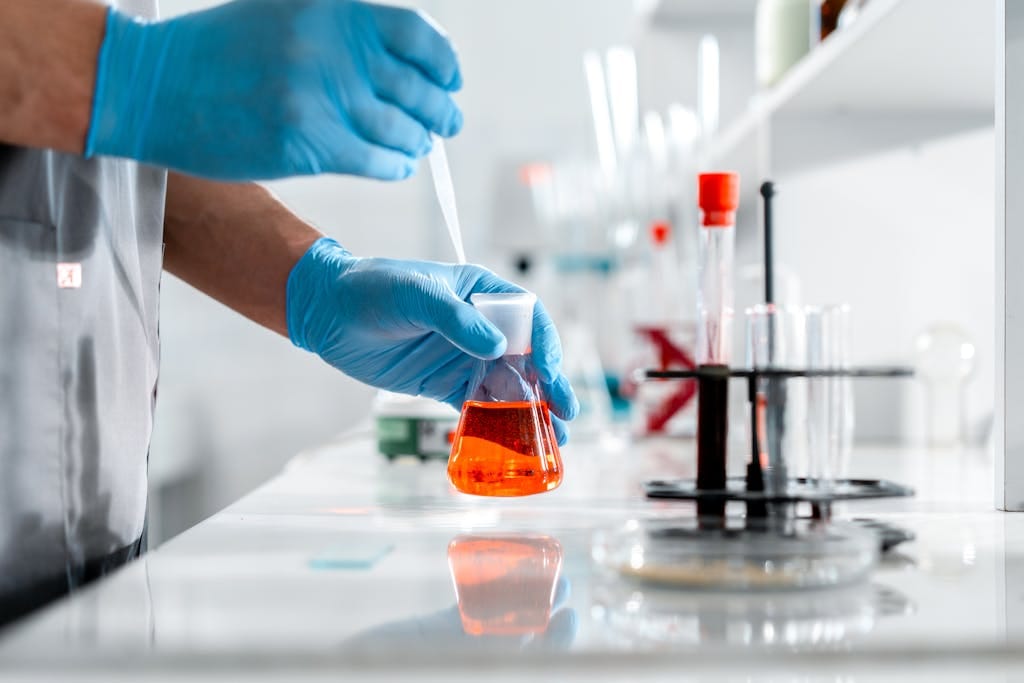
One case study involves a chemical company that specializes in the production of specialty pigments. The company was facing challenges in achieving a consistent particle size distribution in their pigment powders. They implemented a new series of crushers and grinding mills equipped with advanced control systems. These powder equipment allowed for precise adjustment of the grinding parameters such as the speed of the grinding media and the residence time of the pigment in the mill.
Como resultado, they were able to produce pigment powders with a much narrower particle size range. This led to improved color consistency and tinting strength in their final products. Por ejemplo, their pigments were now more suitable for use in high-end coatings and plastics applications where color accuracy is critical.
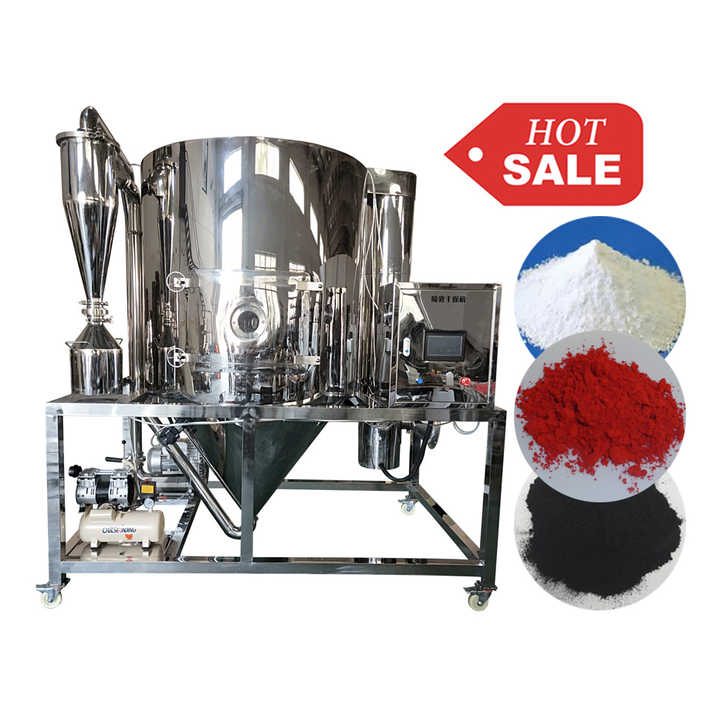
Another example is a chemical plant that manufactures fertilizers. They adopted a new type of granulator that uses a unique extrusion process. This granulator was able to produce fertilizer granules with enhanced durability and controlled release properties. The granules were less likely to break during handling and transportation, reducing product loss. The controlled release feature allowed for a more efficient release of nutrients into the soil over an extended period, improving the effectiveness of the fertilizer. This innovation not only increased the quality of their product but also gave them a competitive edge in the market.
In the production of polymers, powder equipment such as twin-screw extruders has revolutionized the process. These extruders can handle a wide range of polymer powders and additives, precisely mixing and compounding them to create customized polymer blends. A chemical company was able to develop a new line of flame-retardant polymer composites using this powder equipment. The twin-screw extruder allowed for the uniform dispersion of the flame-retardant additives throughout the polymer matrix, ensuring consistent fire resistance properties in the final product. This enabled the company to enter new markets for applications in the electronics and construction industries where fire safety regulations are strict.
A chemical manufacturer of catalysts also benefited from powder equipment advancements. They installed a high-precision sieving and classification system. This system allowed them to separate catalyst powders based on their particle size and activity. By ensuring that only the particles with the desired characteristics were used in their catalytic reactions, they achieved higher reaction efficiencies and selectivity. This led to reduced waste and lower production costs, as well as improved product quality in the chemicals produced using the catalysts.
In conclusion, these case studies demonstrate how powder equipment is transforming the chemical industry. By enabling better control over particle size, forma, and composition, powder equipment is driving innovation, improving product quality, and enhancing the competitiveness of chemical companies in a global market. As technology continues to advance, the role of powder equipment in the chemical industry is set to become even more significant.