Nozzle Atomizer vs Rotary Atomizer in Spray Dryers Which Is Better
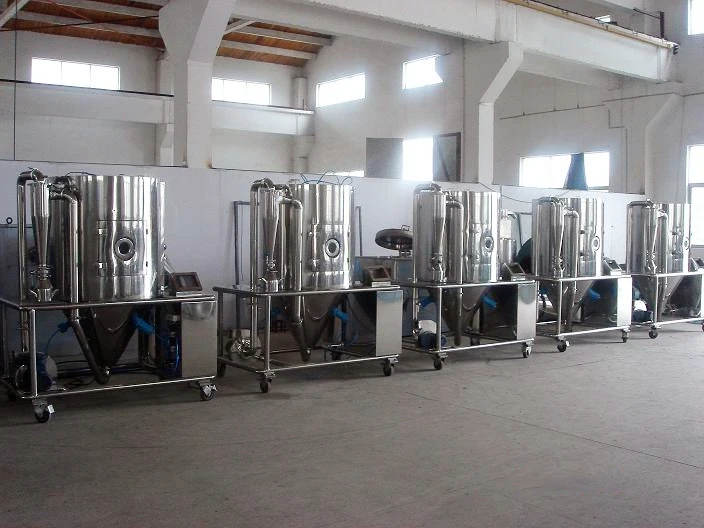
Choosing the best spray dryer atomiser for spray drying depends on your specific needs. Spray dryers operate differently based on droplet size, energy consumption, and maintenance requirements. Recent computer studies reveal that rotary and nozzle spray dryer atomisers produce different spray patterns and drying outcomes. This impacts powder quality and overall process efficiency. Experts evaluate droplet size, uso de energía, and the atomiser’s ability to handle various feed types. Using the right spray dryer atomiser ensures consistent results every time. Selecting the appropriate atomiser significantly influences the spray drying process and the final product quality.
Control de llave
Nozzle atomizers make droplets that are almost the same size. They save energy and need less fixing. This makes them good for small or medium spray drying jobs.
Rotary atomizers work well with thick or lumpy feeds. You can change droplet size by changing the wheel speed. But they use more energy and need more fixing.
Picking the right atomizer depends on your feed type. It also depends on how much you want to make and what powder quality you need. This helps save energy and gives steady results.
Nozzle atomizers make powder that is more even. This is important for food and medicine. Rotary atomizers are better for big jobs and tough feeds.
Cleaning often and using the right settings help both atomizers work well. This helps you get the best powder every time.
Quick Comparison
Diferencias clave
You need to know how each atomization method works. This helps you pick the best spray dryer atomiser. The table below shows how nozzle and rotary atomizers are different in spray drying:
Factor | Nozzle Atomizer | Rotary Atomizer |
---|---|---|
Droplet Size | Makes droplets that are mostly the same size. The size depends on the nozzle and pressure. | You can change droplet size by changing the wheel speed. The droplets are not all the same size. |
Uso de energía | Uses less energy. Two-fluid nozzles need compressed air, which costs more. | Uses more energy because of the fast-spinning wheel. If the feed is salty, it can use 10% less energy. |
Maintenance | Has a simple design and needs less fixing. | Has more parts and needs more fixing because of moving pieces. |
Cost | Costs less at first and to run. Some types need compressed air, which costs extra. | Costs more at first and to fix. The shaft and bearings can break more often. |
Application Suitability | Works best for thin liquids and making lots of powder. | Good for thick or chunky feeds. Also good for things that can’t get too hot. |
Consejo: Think about how well the spray dryer atomiser controls droplet size and saves energy before you choose.
Nozzle atomizers use pressure or air to make droplets. They are good for making even droplets and saving energy. They work well in big spray dryer atomiser systems.
Rotary atomizers have a spinning wheel that throws out the liquid. You can change the droplet size by changing the wheel speed. Pero, they use more energy and need more fixing.
Nozzle atomizers usually make more even droplets. Rotary atomizers are better for hard-to-handle feeds and let you control atomization better.
Rotary atomizers cost more because they are more complicated. Pero, they are good for thick or heat-sensitive materials.
Picking the right spray dryer atomiser helps you get the best powder and saves energy. Each atomizer has its own strengths. You should match the atomization method to what you need.
Nozzle Atomizer
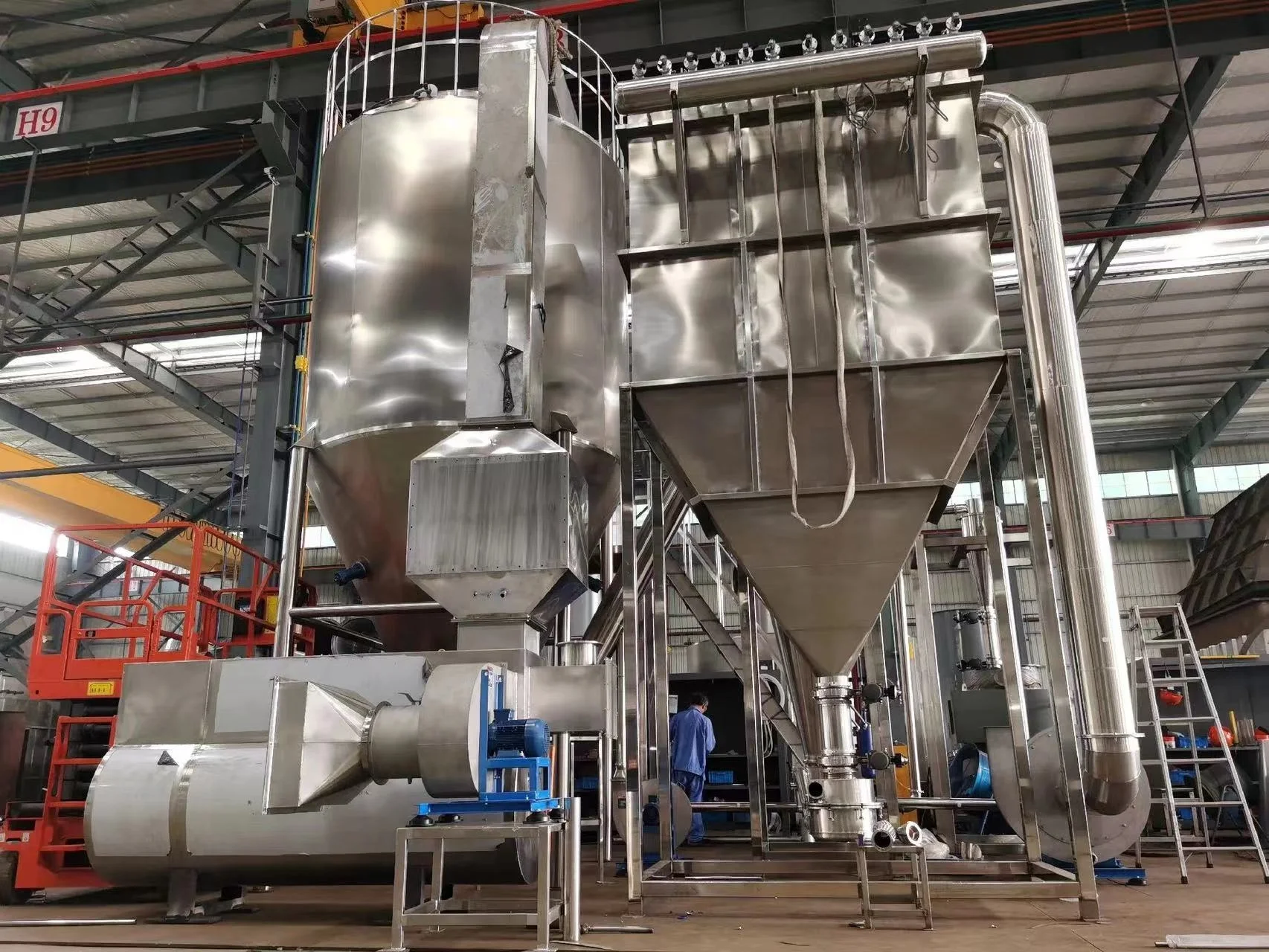
Cómo funciona
A nozzle atomizer uses high pressure or compressed air. This breaks the liquid feed into small droplets. The liquid goes through a tiny hole. The force turns the liquid into a spray. The spray makes a mist of droplets in the drying chamber. The way the atomizer works controls droplet size. Droplet size is important for making even particles and drying well. Engineers use pressure nozzles or two-fluid nozzles. They pick based on what the feed is like. Studies show that more gas flow or pressure makes smaller droplets. Smaller droplets help control how the droplets form. This also makes drying work better. Diagrams of swirl flow nozzles and multi-nozzle heads show how inside parts change droplet spread and atomization. Tests prove nozzle atomizers can make droplets that are almost all the same size. This helps get even particle size in the final powder.
Pros y contras
Nozzle atomizers have many good points in spray drying:
They use less energy than rotary atomizers, especially in big systems.
They make even particle sizes because they control droplet size well.
They need less fixing because they have fewer moving parts.
They save money for big spray dryer jobs.
They work with many types of feed, so they help many industries.
En 2023, nozzle atomizers made up encima 38% of the spray dryer market. They are popular because they work well and keep food and medicine products good.
But nozzle atomizers also have some bad points:
They do not work as well with thick feeds. Thick feeds need more gas pressure to work right.
Needing higher pressure can make them hard to use with some materials.
They have a smaller spray angle than rotary atomizers. This can change how well they cover the drying chamber.
If the feed is thick, the flow inside can get unstable. This makes droplet sizes less even and drying less uniform.
Studies show nozzle atomizers can save up to 29% energía compared to some other nozzles. But you must set the atomizer just right to keep it working well and making even droplets. How well the atomizer works depends on pressure, feed type, and nozzle design. If used the right way, a nozzle atomizer gives good efficiency, even droplet size, and high-quality powder.
Rotary Atomizer
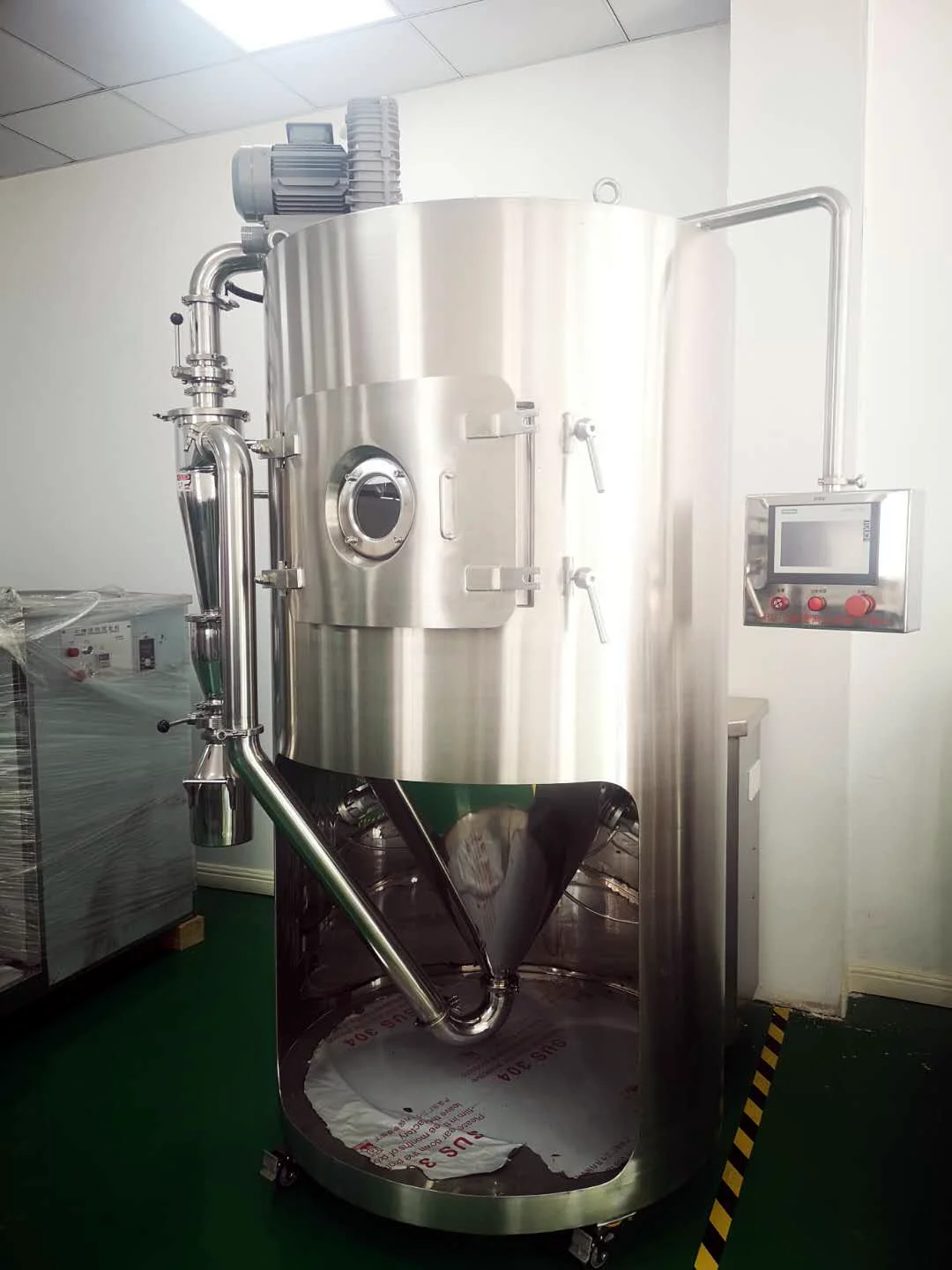
Cómo funciona
A rotary atomizer uses a spinning disc or wheel. The disc spins very fast. Liquid goes into the middle of the disc. The spinning pushes the liquid out to the edge. The liquid spreads into a thin layer as it moves. When it reaches the edge, the disc throws the liquid off. This makes a spray of small droplets. Hot gas in the drying chamber hits these droplets. The heat makes the droplets dry quickly and turn into powder. You can change the disc speed to make bigger or smaller droplets. This helps control the spray and works for many types of feed. It can handle thick or chunky materials too.
How well it works depends on a few things. El amount of liquid, the heat of the gas, and the shape of the atomizer all matter. These things change how big the droplets are and how fast they dry. Rotary atomizers can work with different gas flows. They can use gas that moves in the same or opposite direction as the droplets. This makes them good for things that cannot get too hot. The spray makes droplets of many sizes. This can change how good the powder is.
Pros y contras
Rotary atomizers have some good points in spray drying:
They can work with many kinds of feed, even thick or chunky ones.
You can change the droplet size by changing how fast the disc spins. This lets you control the spray very well.
They are good for things that cannot handle high pressure or too much heat.
Industry reports say rotary atomizers can be used in small or big jobs. They can handle from half a liter to over 10,000 liters each hour. Big companies like GEA Group and SPX Flow make these machines better. They work on saving energy and making the machines last longer.
But rotary atomizers also have some bad points:
They need more fixing because they have more moving parts.
They cost more to buy than nozzle atomizers.
The spray makes droplets of many sizes, so the powder may not be even.
Aspecto | Details |
---|---|
Production Scalability | Can handle from 0.5 to over 10,000 liters per hour |
Industry Applications | Used in food, medicamento, and chemical factories; good for dairy, plant proteins, fatty or thick products, and medicine |
Technological Innovations | Can change speed, use smart sensors, and warn when fixing is needed |
Equipment Longevity Factors | Saves energy, uses robots, keeps heat, and cleans easily |
Leading Manufacturers | GEA Group, SPX Flow |
Market Trends | More money spent on saving energy, using robots, and making bigger machines; more use in new countries |
Nota: Rotary atomizers are flexible and can be used for many jobs, but they cost more and need more care.
Comparison
Droplet Size
Choosing the right spray dryer atomizer helps control droplet size. Nozzle atomizers push liquid through a small hole using high pressure. This makes droplets that are almost the same size. You can change the pressure or nozzle shape to get the droplet size you want. This helps make powder particles that are even. Rotary atomizers use a spinning disc to throw out the liquid. The speed of the disc changes the droplet size. Faster spinning makes smaller droplets. Rotary atomizers make droplets in many sizes, not just one. This means the powder can have different particle sizes. Having even droplets is important for drying and powder quality. It helps the product dry the same way and gives better powder.
Nozzle atomizers make even droplets, so powder shape and drying are easier to control. Rotary atomizers let you change things more, but the droplets are less even.
Uso de energía
Saving energy is important when using spray dryers. Nozzle atomizers use less energy because they use pressure, not fast motors. This makes them good for big spray drying jobs. Rotary atomizers need strong motors to spin the disc fast. This uses more energy. Sometimes, rotary atomizers dry things faster because they make smaller droplets. This can help save some energy. New spray dryers use smart controls to set the best atomizer settings. This helps save energy too. Cleaning and checking the machines often also keeps uso de energía bajo.
Nozzle atomizers: Use less energy and work well with thin feeds.
Rotary atomizers: Use more energy, but can dry better with good droplet making.
Maintenance
How much care each atomizer needs is different. Nozzle atomizers are simple and have fewer moving parts. You need to check for blockages and worn holes to keep them working well. Cleaning and looking at them every day stops problems and saves time. Rotary atomizers have more parts, like the spinning disc and bearings. These need to be checked for dirt, shaking, and damage. Rotary atomizers need daily checks and more careful weekly checks, especially in big spray dryers.
Nozzle atomizers: Easy to take care of, less time stopped, but can get clogged.
Rotary atomizers: Need more checks and cleaning, but smart tools can help stop long breaks.
Capacidad
How much each atomizer can handle matters a lot. Rotary atomizers are best for big jobs. They can handle lots of liquid and work up to 40 tons each hour. They are good for thick or chunky feeds, so they fit big factories. Nozzle atomizers, especially two-fluid ones, can’t handle as much. They work best with thin or not-too-thick feeds and when you need even droplets.
Atomizer Type | Typical Capacity Range | Feed Suitability |
---|---|---|
Nozzle Atomizer | Low to moderate (limited for two-fluid) | Thin to moderately viscous |
Rotary Atomizer | Alto (up to 40 t/h) | Thin, viscous, or particulate |
Rotary atomizers are strong for big spray dryer jobs. Nozzle atomizers are better for small jobs that need even powder.
Cost
Cost means both buying and running the atomizer. Nozzle atomizers cost less to buy and use, especially for small spray dryers. They also cost less to fix because they are simple. Rotary atomizers cost more to buy and fix because they have more parts. But they are worth it for big jobs or hard feeds.
Nozzle atomizers: Cheaper to buy and fix, good for saving money.
Rotary atomizers: Cost more, but needed for big or special spray dryer jobs.
Powder Quality
Powder quality depends on droplet size, el secado, and atomizer type. Nozzle atomizers make powder with even particle sizes. This helps the powder flow well and keeps the right moisture. It is important for food and medicine companies. Rotary atomizers can work with many feeds and make powder with different particle sizes. This is good for some jobs, but the powder may not be as even. Both atomizers change how the powder looks and works, which matters for spray dryer products.
Quality Metric | Nozzle Atomizer | Rotary Atomizer |
---|---|---|
Uniform, controlled by pressure | Variable, controlled by disc speed | |
Flowability | Alto | Moderate to high |
Bulk Density | Consistent | Can vary |
Contenido de humedad | Well controlled | Bien, but may vary with droplet range |
Suitability | Best for strict quality requirements | Best for flexible, high-capacity needs |
Pick the atomizer that matches the powder quality you want and the spray dryer job you have.
Applications in Spray Drying
Small-Scale Production
Small-scale spray drying is done in labs or small plants. These places use spray dryers that handle less than 100 kg each hour. People pick nozzle atomizer applications to control droplet size and dry gently. This keeps important parts safe in medicine and special foods. Ultrasonic nozzles are also used in small spray drying. They make droplets like those in big spray dryer systems. This helps when moving to bigger machines and keeps product quality the same. Important things like atomization pressure, inlet temperature, and slurry flow rate affect how well drying works. Moving the nozzle in a circle spreads droplets better and helps dry evenly. Computer models help improve these things, so fewer expensive tests are needed.
Nozzle atomizer applications: Great for research, new products, and when quality must be high.
Rotary atomizer applications: Not used much because cleaning is hard and fixing takes time.
Large-Scale Production
Big factories use rotary atomizers for making lots of powder. Rotary atomizer applications are best in big spray dryer systems. They can handle 200 liters or more each hour. Rotary atomizers work with many feed rates and thick liquids. This makes them good for food, milk, and chemical spray drying. Rotary atomizers keep working well even with lots of solids. Nozzle atomizers are also used in big jobs, mostly when many nozzles work together. But each nozzle can only handle a little at a time, so rotary atomizers are better for big, nonstop jobs.
Atomizer Type | Key Advantages | |
---|---|---|
Nozzle | Small to moderate | Precise control, easy cleaning |
Rotary | Large-scale production | High throughput, flexibility |
Viscous or Particulate Feeds
Spray drying often uses thick or chunky feeds. Rotary atomizers are good for these by changing disc speed and feed rate. This lets rotary atomizers keep drying well and working fast. Nozzle atomizers, especially two-fluid ones, can also dry thick feeds. They do this by changing gas flow and pressure. Operators can change droplet size and powder shape by adjusting these things. Both types need the right mix of feed thickness, flow, and atomization to get the powder they want.
Consejo: Changing atomization settings helps control droplet size and makes drying better for tough feeds.
Heat-Sensitive Products
Heat-sensitive products need gentle spray drying to stay good. Nozzle atomizers give exact droplet size control, which keeps the product safe. Operators can change pressure and flow to control particle size and drying speed. Special nozzle designs, like ink-jet heads, make even droplets and better powder. Co-current spray drying, where hot air and droplets move together, helps protect heat-sensitive stuff. Rotary atomizers can also dry heat-sensitive feeds, but nozzle atomizers give more control for these jobs.
Nozzle atomizers: Best for medicine, lácteos, and bioactive products.
Rotary atomizers: Used when you need to make a lot and need flexibility.
Spray drying keeps getting better, with new trends for saving energy and making atomizers work well. Operators pick atomizers based on how much they need to make, what the feed is like, and what the product needs to be. This helps them work better and make good powder.
Picking the right atomizer for a spray dryer is important. It changes how well the machine works and how much energy it uses. Studies show nozzle atomizers are best when you need small, even droplets. They also work well for small or medium jobs. Rotary atomizers are better for big jobs. They can handle thick or chunky feeds and make more powder. Real-life examples show that using the right atomizer helps save energy and makes better powder.
Nozzle Atomizer | Rotary Atomizer | |
---|---|---|
Performance | Alta eficiencia, precise control | High capacity, flexible performance |
Efficiency | Energy-saving, low maintenance | Handles viscous feeds, robust design |
Spray Drying Suitability | Small to medium scale, uniform powder | Large scale, varied feed properties |
To get the best results, pick an atomizer that fits your spray dryer size, the type of feed, and what you want to achieve. This helps you save energy and get good powder every time.
Preguntas más frecuentes
What is the main difference between a nozzle atomizer and a rotary atomizer?
A nozzle atomizer uses pressure to make even droplets. A rotary atomizer has a spinning disc that makes droplets in many sizes. Each one works best for different kinds of feeds and job sizes.
Which atomizer is easier to maintain?
Nozzle atomizers have fewer parts that move. They are easier to take care of. Rotary atomizers have spinning parts, so they need more checks.
Can rotary atomizers handle thick or chunky feeds?
Sí, rotary atomizers can work with thick or chunky feeds. Their design lets them handle tough materials. Nozzle atomizers can get clogged by these feeds.
Which atomizer produces more uniform powder?
Nozzle atomizers make powder that is more even. They control droplet size better. Rotary atomizers make powder with many different sizes.
How does atomizer choice affect energy use in spray drying?
Nozzle atomizers usually use less energy. Rotary atomizers need more power to spin the disc. How much energy you use depends on the feed and job size.
Consejo: Pick the atomizer that fits your product and process to get the best results.