Detailed Overview of Spray Drying Technology
Spray Drying Technology
Spray dryers are industrial machines used to transform liquids into powders or granules in a single step. The liquid is atomized into tiny droplets, and these droplets are then dried using a hot air stream to remove moisture. The result is a fluid powder that is easy to transport and package. Spray drying is widely used in the food, pharmaceutical, and chemical industries due to its high efficiency, adaptability, and consistent product quality.
The History and Working Principle of Spray Dryers
History of Spray Drying
Spray drying was first employed by French engineer Alexis Millardet in the 19th century to create dried wine yeast for the wine industry. However, the process didn’t become widely used until the mid-20th century. The first industrial spray dryer was developed in the 1930s. Early spray dryers used nozzle atomizers, and it wasn’t until decades later that rotary atomizers were introduced. The technology saw limited commercial use until the 1920s due to the simplicity of early designs and operational challenges. Over time, spray drying technology has evolved to meet the needs of various industries.
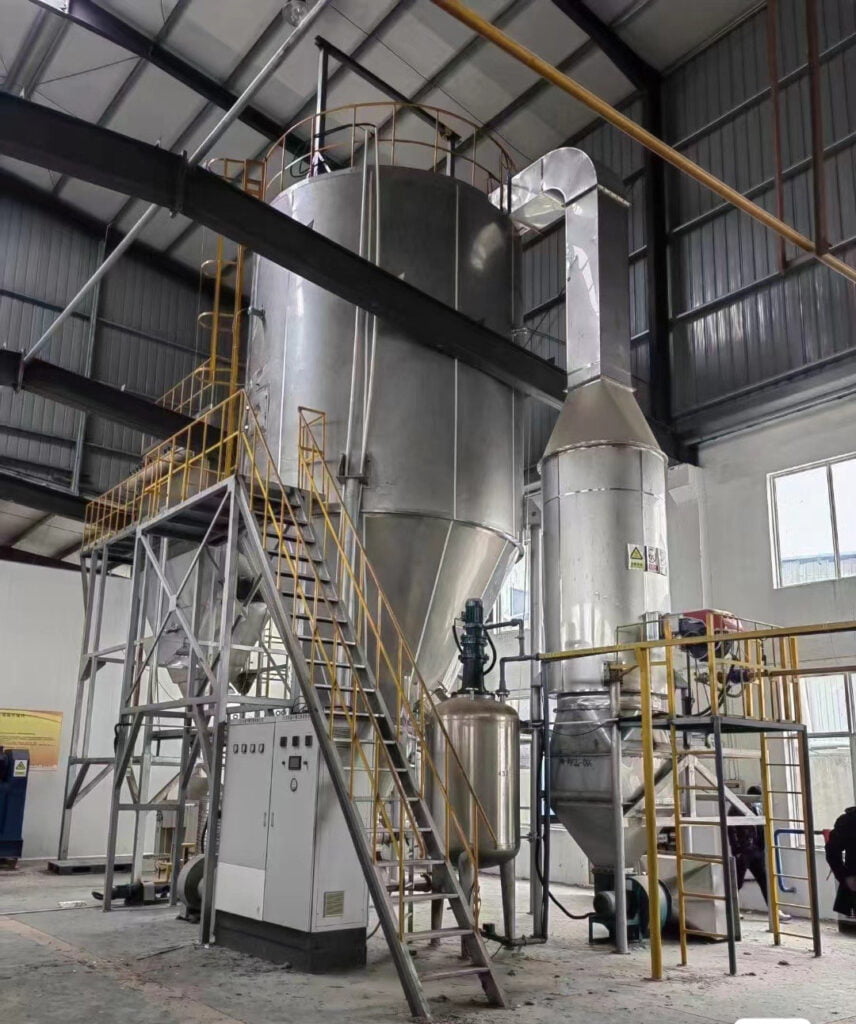
How Spray Dryers Work
Let’s discuss the working principle of a spray dryer. The most common spray dryers consist of several key components:
- A spray system
- A drying chamber
- A hot air stream
- A collection system
Here’s how these components work together:
- Feed Preparation: The components are mixed to create the liquid feed, adjusting viscosity and homogenizing the mixture.
- Atomization: The liquid is pumped into a spray nozzle or spinning disk, where it is atomized into fine droplets.
- Dehydrating: The droplets are introduced into the drying chamber, where they are quickly dried by the hot air stream. The temperature and flow rate of the hot air are carefully controlled to achieve the desired particle size, morphology, and residual moisture content.
- Collection System: The dried powder is collected by a system, typically using centrifugal forces with a cyclone or a bag filter, and can be packaged or further processed.
The key to spray drying is the rapid evaporation of the liquid droplets in the hot air stream. The drying rate is influenced by several factors, including droplet size, temperature, air velocity, and the product’s moisture content. Controlling these factors ensures a consistent, high-quality product.
Types of Spray Dryers and Their Applications
There are several types of spray dryers available, and the choice depends on the properties of the liquid feed, the desired final product, and the production capacity required.
- Rotary or Centrifugal Atomization: Uses a spinning wheel to atomize the liquid into droplets. This type of spray dryer is versatile and can handle high viscosity applications.
- Pressure Nozzle Atomization: Uses a high-pressure pump to create a consistent, homogenous powder. It is commonly used in the food and dairy sectors.
- Two-Fluid Nozzle Atomization: Uses a gas (usually compressed air or steam) to atomize the liquid. This type of nozzle is often used for pilot dryers.
- Combination of Spray Dryers and Fluidized Beds: Integrates fluid beds with spray dryers to remove small quantities of moisture or cool the product.
- Closed Cycle: Uses nitrogen as the drying medium instead of air, suitable for products susceptible to oxidation or when the solvent is an organic liquid.
Advantages of Spray Drying
- Flexibility: Spray drying can produce powders from a wide range of liquid feeds, making it cost-effective for various products such as food ingredients, pharmaceuticals, chemicals, and cosmetics.
- Superior Product Quality: The process ensures uniform particle size and stability, which is crucial in industries like food, pharmaceuticals, and cosmetics.
- Preservation of Active Ingredients: Suitable for industries where preserving the potency and efficacy of active components is essential.
- Versatility: Can be customized for different liquids and suspensions, allowing for a diverse range of powders.
- Reduction of Contaminants: Helps reduce bacteria and other microbes, important in food and pharmaceutical industries.
Industrial Applications of Spray Dryers
Spray drying technology is versatile and used in various industries:
- Food: Used for making instant coffee, tea, milk powders, egg products, infant formula, and more. It preserves flavor, aroma, and color while minimizing contaminants.
- Pharmaceutical: Used for creating powders, granules, tablets, and encapsulating active substances.
- Chemical: Used for catalysts, pigments, detergents, and drying solvents and other chemical solutions.
- Agricultural: Used for animal feed, fertilizer, and pesticides.
- Biotechnology: Used for recombinant proteins, vaccines, and other biopharmaceuticals.
- Environmental: Used for treating wastewater, solid waste, and air pollution.
- Cosmetic: Used for producing cosmetic powders and personal care products.
- Materials for Lithium-Ion Batteries: Emerging market for producing powders for cathode and anode materials in EV batteries.
Disadvantages of Spray Drying
- Limited Feed Viscosity: Only feedstocks with viscosity lower than 500 centipoises can be dried, requiring dilution of some feeds.
- High Capital Cost: Expensive to purchase and operate due to the high evaporation rate.
- High Energy Consumption: Consumes a lot of energy for heating air and atomizing feed.
- Operational Safety: Requires explosion protection systems and fire safety systems due to the risk of deflagration.
Despite these disadvantages, the return on investment in spray drying technology is substantial, and continuous innovations mitigate many of these limitations.
How to Make Spray Drying Viable for Your Business
Choosing the right equipment and supplier can optimize cost-benefit. Innovative spray drying technology, such as high-speed rotary atomizers with magnetic bearing technology, offers flexibility and low maintenance, recouping investments efficiently.
Conclusion
Spray drying is a widely recognized technology with numerous advantages over other drying methods. While it has its complexities and high technical requirements, the benefits often outweigh the drawbacks. Carefully weighing the pros and cons will help determine if spray drying suits your application.
For more information on drying equipment, visit our Drying Series, Conduction Dryer, and Hot Air Transfer Dryer pages. Whatever help you need, please feel free to contact us on whatsapp