Advantages and Disadvantages of Fluid Bed Granulation in Pharmaceuticals
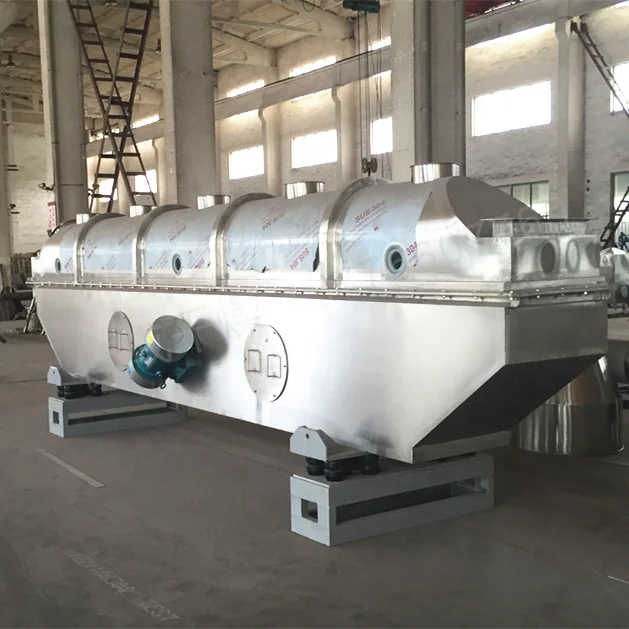
Granulation is very important in making medicines. It helps powders become easier to handle and better in quality. Fluid bed granulation is a new way to make even and easy-to-move granules. These granules are needed to make tablets the same every time. The process makes the average particle size two or three times bigger. You can see this in the table below. This helps keep the granules the same size.
Parameter | Experimental (600 rpm) | Experimental (900 rpm) |
---|---|---|
Mean Particle Diameter (μm) | 3.16 | 2.35 |
Standard Deviation (μm) | 1.64 | 1.36 |
Knowing the good and bad sides of fluid bed granulation helps people pick the right way to make medicine. Fluidized bed granulation has many good points. But it also has some problems.
Key Takeaways
Fluid bed granulation mixes, sprays, and dries powders in one machine. This makes making medicine faster and easier.
This process makes granules that flow well and are the same size. This helps tablets stay the same and easy to use.
You must control air flow, temperature, and binder spray carefully. If not, you can get sticky lumps or broken granules.
The machine keeps workers safe by lowering dust and germs. It also helps with strict checks for safe medicine.
Not all powders work well with this method. Free-flowing powders are best. Sticky or big powders can cause problems.
Fluid Bed Granulation Overview
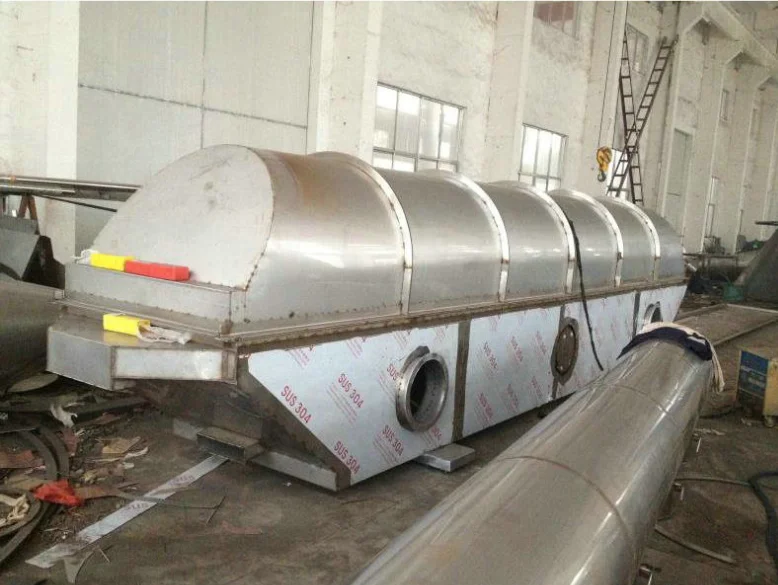
Process Basics
Fluid bed granulation is a newer way to make granules for medicine. First, powders are mixed together in a special machine called a fluidized bed granulator. The machine blows air to lift and mix the powder. Next, workers spray a binder liquid onto the moving powder. The binder helps the powder stick and form bigger pieces called granules. After spraying, the machine dries the wet granules with warm air. This step takes away water and makes the granules strong and easy to move.
Many things can change how well granulation works. These include how fast the binder is added, how hot the air is, how fast the air moves, and how high the spray nozzle is. Each thing must be watched closely. The fluidized bed granulator lets workers check moisture and granule size as they work. Near-infrared (NIR) spectroscopy checks moisture without hurting the granules. Other tools, like Focused Beam Reflectance Measurement, watch granule size during the process. These tools help workers change settings and keep granules the same every time.
Note: It is important to manage risks in fluid bed granulation. Workers use data from the machine to control risks and make sure each batch is good.
Role in Pharmaceuticals
Fluid bed granulation is very important in making medicine. The process makes granules that flow well and press into tablets easily. This helps companies make safe and even medicines. The fluidized bed granulator mixes, makes, and dries granules all in one machine. This saves time and keeps more product from being wasted.
Fluidized bed granulation helps powders flow better and makes less dust.
The process helps make lots of medicine by keeping things steady.
The machine lets workers change things quickly to make better products.
Medicine companies use the fluidized bed granulator to follow strict rules. The machine supports process analytical technology, which helps check and improve each batch. This way, companies have better control, make more medicine, and keep it safe.
Advantages and Disadvantages
Process Efficiency
Fluid bed granulation works fast and saves time. The machine mixes, makes, and dries granules all at once. This means workers do not need to move materials as much. Special monitors check temperature, humidity, and particle size as the process runs. The machine can change settings by itself to keep things right. These features help companies make more medicine quickly.
Granules are about the same size, so tablets are better.
The machine uses less energy and solvent than other ways.
Workers can change settings fast to get better results.
But the process needs careful control. If air flow or binder spray changes a lot, it may not work. High pressure drops and granule breakage can also slow things down. Workers must watch closely to stop problems like too much water or spray-drying.
Note: The machine works best when air flow, spray rate, and temperature are controlled.
Granule Quality
The machine makes granules that flow well and are the same size. These granules help make even tablets and less dust. The process gives granules the right strength and density for tablets. Special tools, like near-infrared spectroscopy, help workers keep granule quality high.
Empirical Advantages | Empirical Disadvantages | |
---|---|---|
Top Spray | More porous granules; contained ‘one-pot’ production | Irregular shape; increased spray drying |
Bottom Spray | Smaller, denser, spherical granules; better flow | Slower growth; higher risk of overwetting |
Tangential Spray | Uniform growth; good flow, low friability | Denser granules; material loss; high cost |
Granule quality depends on the machine type and powder used. Hydrophobic powders make rounder, tighter granules but may leave more fines. Hydrophilic powders can limit binder, which affects sticking. The process works best if powders flow well before starting.
Granules from this machine have even size and flow well.
Bulk density and flowability help make steady tablets.
Still, making special granules for certain needs can be hard. If settings are wrong, granules may get too hard or too soft.
Safety and Reproducibility
Fluid bed granulation is safe and gives steady results. The machine uses covers and anti-static bags to stop dust. These features keep workers safe from harmful powders. The process helps make each batch the same, which is important for medicine.
The machine is easy to clean and stops contamination.
Monitors check each batch to meet quality rules.
Checking binder and granule size helps keep results steady.
Aspect | Details |
---|---|
Binder concentration, mixing time, granule size, moisture content, blend homogeneity | |
Validation Phases | IQ: machine specs; OQ: function under varied conditions; PQ: output meets quality specs |
Regulatory Focus | Ensures batch-to-batch reproducibility and critical quality attributes |
The machine can make small or big batches with the same results. Similar machines help keep things the same at any size. Rules and checks make sure the process is safe and meets quality needs.
Limitations
Fluid bed granulation has some problems too. The process needs powders that flow well before starting. If the powder does not flow, the machine may not work right. Overwetting can happen, especially with some spray types. Too much water can make granules stick or form lumps.
The machine can lose powder if air flow is too high.
High costs and pricey machines make it hard for some companies to grow.
The process can change if temperature, binder, or air flow changes.
Making special granules for things like drug release or tablet strength can be tough. Extra sensors and models help, but they cost more and make things harder.
Tip: Companies should think about the good and bad sides before picking fluid bed granulation.
Fluid Bed Granulator Features
Equipment Design
A fluid bed granulator has smart parts to help make medicine. The conical expansion chamber slows air in the filter area. This keeps small particles from escaping and helps the filter last longer. The strong agitator moves powder so drying happens everywhere. Top-spray nozzles, shaped like a chandelier, spray binder evenly. Each nozzle has its own pump to cover the whole bed and make the machine work better.
Other important parts are:
Spiraflo bed plate gives even air flow and stops channeling. This keeps fluidization steady.
High-yield filters with pulse cleaning keep the process running and lower product loss.
Flared partitions balance air in coating zones. This lets workers use higher spray rates.
Air handling units clean, dry, and heat air before it goes in the granulator.
Modular design options include explosion-proof systems and remote controls for safety and flexibility.
The table below shows how fluid bed granulator models are different:
Model (BFS series) | Number of product filter bags | Approximate Height (mm) | Number of Tangential Spray Nozzles | Control System |
---|---|---|---|---|
BFS 30 | 4 | ~1980 | 1 | PLC controlled, Touchpanel operated |
BFS 60 | 6 | ~2930 | 2 | PLC controlled, Touchpanel operated |
BFS 120 | 6 | ~3600 | 3 | PLC controlled, Touchpanel operated |
BFS 240 | 9 | ~3920 | 4 | PLC controlled, Touchpanel operated |
BFS 360 | 12 | ~4570 | 5 | PLC controlled, Touchpanel operated |
BFS 480 | 10 | ~4990 | 6 | PLC controlled, Touchpanel operated |
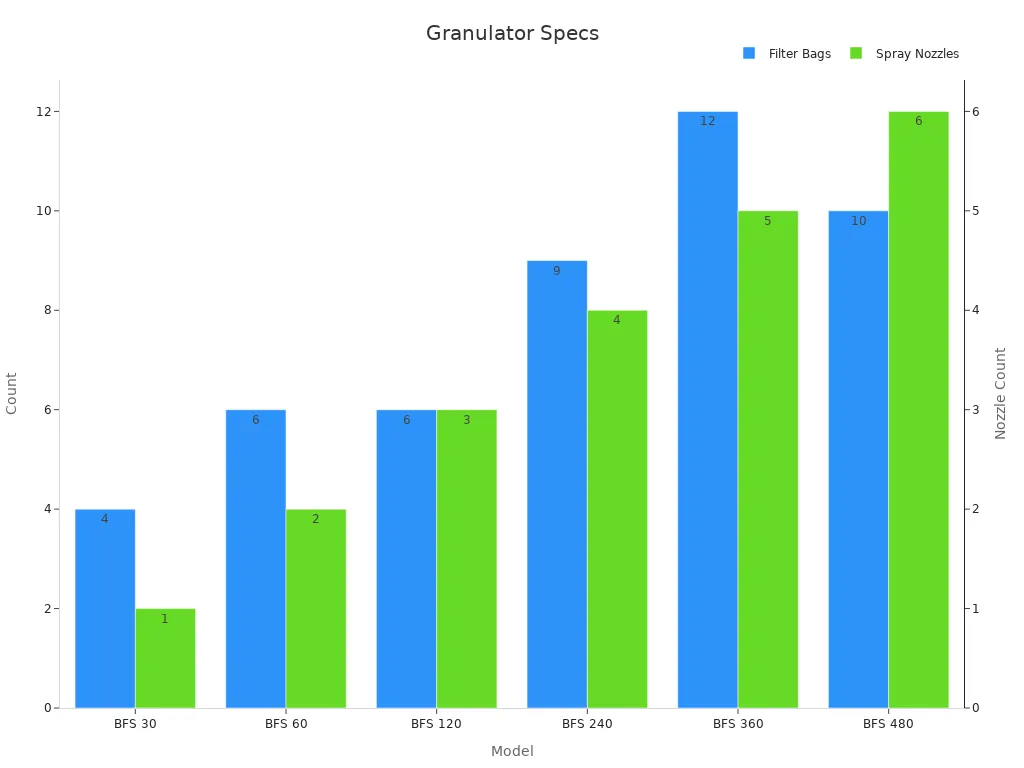
These features help the fluid bed granulator give steady results. It is easy to clean and can be used for different batch sizes.
Process Control
Process control in a fluid bed granulator keeps product quality high. Operators watch things like granule size, density, flow, and moisture in real time. They change air flow, temperature, and spray rate to keep things steady. PID controllers help keep air flow and temperature right. Temperature sensors show when granules grow or dry. Moisture sensors help find when drying is done.
Operators use in-line detectors to check all the time.
Data from air flow, spray rate, and pressure help fix problems fast.
Design of experiments helps find the best settings for each product.
Advanced models use neural networks and fuzzy logic to predict changes. These tools help the granulator make steady batches every time. Good process control means the fluid bed granulator can make safe, high-quality medicine.
Granulation Methods Comparison
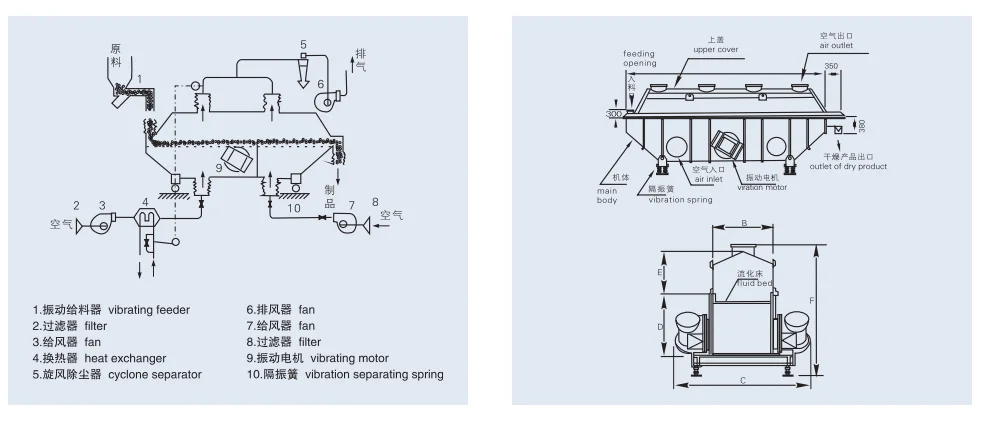
Fluid Bed vs. Wet Granulation with Fluid Bed Granulator
Fluid bed granulation and wet granulation with fluid bed granulator both help make medicine. They work in different ways. Fluid bed granulation uses one machine to mix, spray, and dry powders at the same time. Wet granulation with fluid bed granulator often uses a process that keeps going. Powders move through mixing, spraying, and drying without stopping.
Here is a table that shows some main differences:
Aspect | Fluid Bed Granulation (Single-cell machines) | Wet Granulation Using Fluid Bed Granulators (Continuous) |
---|---|---|
Process Type | Mixing, agglomeration, and drying in one chamber | Continuous dosing, mixing, and drying in sequence |
Mixing and Transport | Random mixing, longer residence time | Granules move by air or gravity, shorter residence time |
Process Parameters Impact | Binder spray and air flow change granule size and moisture | Drying settings affect granule breakage and moisture |
Challenges | Hard to control all steps in one chamber | Granules can break during transfer and drying |
Product Properties | Size and moisture controlled by settings | Moisture drops with drying; size can vary |
Industry Application | Less common due to complexity | Used more in continuous manufacturing |
AI tools now help fluid bed granulation work faster and use less energy. Some companies have made drying time almost an hour shorter for each batch. They have also saved thousands of kilowatt-hours every year. These changes make the process better and help keep granule quality the same.
Fluid Bed vs. Other Granulation
Granulation can use different machines like high-shear mixers, twin-screw granulators, or roll compactors. Each way makes granules with different shapes and strengths. Fluid bed granulation makes granules that are more porous and not as even. High-shear granulation makes rounder, denser granules that flow better.
Granulation Method | Granule Shape | Porosity | Bulk Density | Flowability | Key Findings |
---|---|---|---|---|---|
High-shear | Spherical | Low | High | Better | Denser, better flow, needs extra drying |
Fluidized-bed | Irregular | High | Low | Lower | More porous, dries as it granulates |
Continuous granulation methods, like twin-screw or fluid bed, help companies make bigger batches without problems. These methods use the same machines from lab to factory, so making more is easier. Wet granulation with fluid bed granulator and other continuous ways often give better granules and tablets than old batch methods. Companies can also change granule size and strength by changing screw speed or water amount.
Tip: Pick the right granulation method based on the medicine, the granule properties needed, and how much you need to make.
Implementation
Material Suitability
Picking the right materials is very important for fluid bed granulation. Scientists check many powder features before they start. Particle size distribution is a big factor. If powders have many different sizes, granules can turn out uneven. Porosity in the powder and between particles matters too. It affects how much binder and water the powder can take in. If the powder soaks up too much liquid, granules might get too big or sticky.
Experts use the theoretical maximum pore saturation to guess how much water the powder bed can hold. This helps stop overwetting. The liquid-to-solid ratio and how fast the binder is added are important too. These things help control how granules grow and how strong they are. The ideal mixing rule helps scientists know how the mix will act by looking at the densities and mass ratios of each part.
Fluid bed granulation does not work well with powders that are very bulky or stick together a lot. These powders can make it hard for the machine to work right. Modern tools like near-infrared (NIR) spectroscopy let workers check particle size, moisture, and density as they go. These checks help keep the process working well and make sure the material stays in the right range.
Tip: Always test how the powder flows and its porosity before picking fluid bed granulation for a new formula.
Process Monitoring
Watching the process closely keeps fluid bed granulation safe and working well. Operators use special tools to check progress and quality.
Torque measurement shows how hard the blender paddle works. If torque changes, it can mean granules are growing.
Focused-beam-reflectance measurement checks wet granule size without stopping the process.
Acoustic emission monitoring uses microphones to listen for changes in granule movement. This helps find the end point.
Drag flow force sensors measure how easily powder moves, which links to powder quality.
The table below lists common monitoring tools and what they check:
Monitoring Technique | What It Measures | How It Helps |
---|---|---|
Near-Infrared Spectroscopy (NIRS) | Particle size, moisture, active ingredient amount | Real-time quality checks, robust predictions |
Torque Measurement | Blender paddle resistance | Tracks granulation progress |
Focused-Beam-Reflectance Measurement | Wet granule size | Non-contact, real-time size monitoring |
Acoustic Emission | Sounds from granules | Finds process end point quickly |
Drag Flow Force Sensors | Powder flow and rheology | Monitors flow for process control |
These tools help operators make quick choices and keep each batch the same. Real-time data helps keep product quality high and the process safe.
Fluid bed granulation has many good points for making medicine. It mixes, granulates, and dries powders in one closed machine. This helps stop germs or dirt from getting in. The process makes granules that are even and flow well. These granules are easy to press into tablets. The closed system also keeps workers safe when using dangerous powders.
But there are some problems with this process too:
Limitation | Impact |
---|---|
Low particle density | Tablets might not be strong enough |
Complex operation | Workers must watch air, heat, and spray closely |
Drying can take a long time |
Medicine makers need to think about these good and bad points. They should pick what works best for their product. New tools and better ways to watch the process help make things faster and better.
FAQ
What is fluid bed granulation used for in pharmaceuticals?
Fluid bed granulation turns powders into granules. These granules move better and are easier to press into tablets. Companies use this method to make sure each tablet has the same amount of medicine.
How does fluid bed granulation improve tablet quality?
Fluid bed granulation makes granules that are even and strong. These granules help tablets keep the same size and strength. The process also lowers dust and makes tablets easier to handle.
What are the main challenges with fluid bed granulation?
Powders need to flow well before starting.
Too much water can make sticky lumps.
The machines can cost a lot.
Can fluid bed granulation handle all types of powders?
Powder Type | Suitability |
---|---|
Free-flowing | Good |
Sticky or bulky | Poor |
Some powders do not work well in the machine. Sticky or bulky powders can cause problems.